Content Menu
● The Evolution of Powder Supply Systems
>> From Manual Handling to Automation
>> Industry 4.0 and Digitalization
● Key Innovations in Powder Supply Systems
>> Enclosed and Sealed Transfer Systems
>> Advanced Conditioning and Flow Control
>> Precision Feed and Dosing Systems
>> Explosion Mitigation and Static Control
>> Collaborative Robotics and Automation
● Innovations in Powder Production and Morphology
>> Spherical Powder Technology
>> Multi-Material and Functional Powders
>> AI-Driven Powder Design
● Integrated and On-Demand Powder Production
>> DirectPowder and System of AM Systems
>> Sustainable and Eco-Friendly Solutions
● Flexibility, Personalization, and Future Trends
>> Flexible and Modular Systems
>> Personalized and Custom Packaging
>> Collaborative Innovation Ecosystems
● Challenges and Opportunities Ahead
● Frequently Asked Questions
● Citations:
Powder supply systems are at the heart of modern manufacturing, enabling industries from pharmaceuticals to aerospace to produce high-quality products with precision and efficiency. As global demand for advanced materials grows, so does the need for innovative powder handling, storage, and delivery solutions. This article explores the top innovations transforming powder supply systems, examining their impact on productivity, sustainability, safety, and customization.
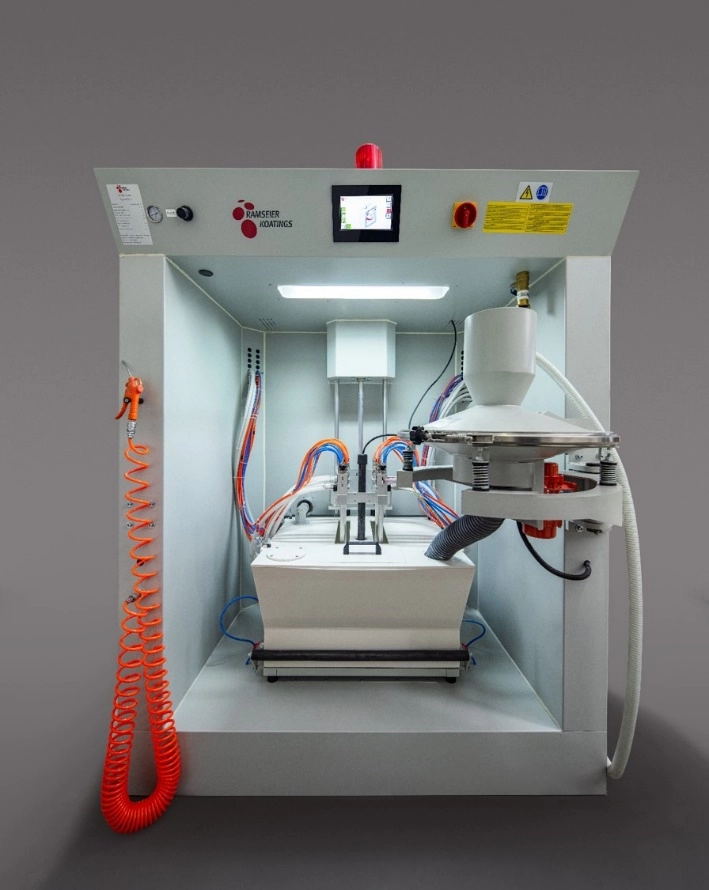
The Evolution of Powder Supply Systems
From Manual Handling to Automation
Historically, powder supply relied heavily on manual labor and open-air processes. This approach was not only labor-intensive but also introduced risks of contamination, inconsistent material flow, and safety hazards. The shift toward automation and enclosed systems marks a significant leap forward, reducing human intervention, improving consistency, and enhancing workplace safety.
Industry 4.0 and Digitalization
The integration of Industry 4.0 technologies—such as the Internet of Things (IoT), big data analytics, and advanced process control—has revolutionized powder supply systems. These digital tools enable real-time monitoring of equipment, predictive maintenance, and data-driven optimization of operations. As a result, manufacturers can minimize downtime, optimize resource use, and improve product quality.
Key Innovations in Powder Supply Systems
Enclosed and Sealed Transfer Systems
One of the most impactful innovations is the move from manual, open-air handling to sealed gas and vacuum-based transfer systems. These systems:
- Preserve powder quality by limiting exposure to air and contaminants.
- Enhance worker safety by reducing direct contact with hazardous materials.
- Minimize material loss and environmental impact.
By maintaining a controlled environment, these systems are especially beneficial for sensitive and reactive powders, such as those used in additive manufacturing and pharmaceuticals.
Advanced Conditioning and Flow Control
Powders can lose their free-flowing characteristics over time due to environmental exposure. Modern conditioning equipment addresses this by:
- Maintaining controlled humidity and temperature conditions.
- Integrating sieving systems to ensure uniform particle size.
- Utilizing vibration and agitation mechanisms to prevent clumping.
These innovations guarantee consistent flow properties, which are critical for high-quality production in sectors like metal additive manufacturing and food processing.
Precision Feed and Dosing Systems
Accurate and consistent powder delivery is essential for downstream processes such as pressing, sintering, or 3D printing. Precision feed systems now offer:
- Tight control over flow rates and composition.
- Automated feedback loops to adjust dosing in real-time.
- Integration with weighing and quality control sensors.
Such systems reduce product defects, improve repeatability, and streamline batch-to-batch consistency.
Explosion Mitigation and Static Control
Handling fine powders—especially metals—introduces risks of combustion and explosion. Innovations in safety include:
- Electrostatic discharge protection.
- Use of non-sparking materials in equipment design.
- Explosion-venting and inert gas suppression systems.
These features are increasingly standard in facilities handling reactive or combustible powders, ensuring compliance with stringent safety regulations.
Collaborative Robotics and Automation
Collaborative robots (cobots) are being integrated into powder processing environments to:
- Automate repetitive tasks such as loading/unloading hoppers and monitoring system parameters.
- Work safely alongside human operators.
- Enhance productivity and reduce labor costs.
Cobots are particularly valuable in hazardous or high-throughput environments, where their precision and reliability drive operational excellence.
Innovations in Powder Production and Morphology
Spherical Powder Technology
Spherical powders have become a cornerstone of advanced manufacturing, offering superior flowability and packing density compared to irregular particles. Key advancements include:
- Gas and Plasma Atomization: These methods produce powders with precise size distribution and enhanced sphericity, crucial for additive manufacturing and thermal spraying.
- Plasma Spheroidization: High-temperature plasma reshapes irregular particles into perfect spheres, improving purity and flow characteristics.
- Centrifugal Atomization: Melting and spinning metals at high speeds to create uniform spherical particles, essential for aerospace and biomedical applications.
These techniques have expanded the range of usable materials and improved the quality of manufactured components.
Multi-Material and Functional Powders
The development of multi-material powders with tailored properties—such as enhanced strength, thermal resistance, or electrical conductivity—enables manufacturers to address specialized application needs. This innovation is particularly significant in the healthcare, energy, and electronics sectors.
AI-Driven Powder Design
Artificial intelligence and machine learning are transforming powder production by:
- Optimizing particle size and morphology.
- Predicting performance characteristics based on process parameters.
- Accelerating the development of new powder formulations.
This data-driven approach reduces development cycles and enhances material performance.
Integrated and On-Demand Powder Production
DirectPowder and System of AM Systems
A major leap in powder supply is the integration of powder production directly with additive manufacturing (AM) systems. The DirectPowder process exemplifies this innovation by:
- Producing powder on-site, on-demand, and tailored to specific requirements.
- Eliminating the need for large inventories and reducing storage costs.
- Enhancing safety by minimizing the time powder is exposed before use.
This approach, known as the "System of AM Systems," optimizes technical, business, and environmental factors by co-locating powder production with the point of use. It is especially valuable in scenarios where logistics are challenging, such as expeditionary manufacturing.
Sustainable and Eco-Friendly Solutions
Sustainability is a driving force in the evolution of powder supply systems. Innovations include:
- Use of biodegradable, compostable, or recycled packaging materials.
- Reduction of waste through precise dosing and minimized overproduction.
- Energy-efficient production methods and reduced transportation needs.
These measures support industry commitments to net-zero emissions and environmentally responsible manufacturing.
Flexibility, Personalization, and Future Trends
Flexible and Modular Systems
Modern powder supply systems are designed for flexibility, enabling manufacturers to:
- Handle a wide range of powder types and particle sizes.
- Quickly switch between products or formulations.
- Integrate with other packaging and processing technologies.
This adaptability is crucial for responding to shifting market demands and customer preferences.
Personalized and Custom Packaging
As consumer demand for unique and customized products grows, powder supply systems are evolving to offer:
- Personalized containers and labeling.
- Customizable dosing and packaging solutions.
- Integration with digital platforms for traceability and customer engagement.
Personalization enhances brand value and meets the expectations of increasingly discerning customers.
Collaborative Innovation Ecosystems
Industry-academia collaborations and public-private partnerships are accelerating progress in powder supply technologies. These ecosystems:
- Foster the exchange of expertise and resources.
- Enable large-scale research and development initiatives.
- Address challenges related to cost, scalability, and environmental impact.
Such collaborations ensure that powder supply systems remain at the forefront of innovation.
Challenges and Opportunities Ahead
While significant progress has been made, challenges remain in scaling up new technologies, managing costs, and ensuring regulatory compliance. However, the continued convergence of digitalization, automation, and material science promises to unlock further advancements in powder supply systems.
Manufacturers who embrace these innovations stand to benefit from:
- Increased operational efficiency.
- Enhanced product quality and consistency.
- Reduced environmental footprint.
- Improved workplace safety.
- Greater responsiveness to market trends.
Frequently Asked Questions
1. What are the main benefits of using enclosed transfer systems in powder handling?
Enclosed transfer systems protect powders from air and contaminants, enhance worker safety, and reduce material loss. They are especially important for sensitive or hazardous materials.
2. How does spherical powder technology improve manufacturing processes?
Spherical powders have superior flowability and packing density, leading to higher-quality components with fewer defects. They are essential for additive manufacturing and applications requiring precise material properties.
3. What role does automation play in modern powder supply systems?
Automation reduces manual intervention, improves consistency, enables real-time monitoring, and enhances safety. It also allows for greater scalability and flexibility in production.
4. How are AI and machine learning impacting powder production?
AI and machine learning optimize particle design, predict performance, and accelerate the development of new powder formulations, resulting in better materials and shorter development cycles.
5. Why is on-demand powder production significant for additive manufacturing?
On-demand powder production eliminates the need for large inventories, reduces storage costs, and improves safety by minimizing powder exposure. It also allows for customization and rapid response to production needs.
6. What sustainability trends are emerging in powder supply systems?
Trends include the use of eco-friendly packaging, waste reduction through precise dosing, and energy-efficient production methods, all supporting industry goals for reduced environmental impact.
7. How do collaborative robots enhance powder processing operations?
Collaborative robots automate repetitive or hazardous tasks, improve precision, and can work safely alongside humans, increasing efficiency and reducing labor costs.

---
Citations:
[1] https://capitalresin.com/14-new-trends-in-powder-bulk-processing/
[2] https://jenike.com/innovations-handling-and-storing-metal-powders-modern-manufacturing-industries/
[3] https://www.vtops.com/future-of-dry-powder-filling-packaging-technology/
[4] https://www.metalpowderworks.com/mpw-in-the-news/the-system-of-am-systems
[5] https://ebeammachine.com/discover-the-latest-trends-in-spherical-powder-technology-for-2025/
[6] https://www.coatingsworld.com/contents/view_online-exclusives/2024-08-21/powder-coatings-innovations/
[7] https://www.coast2coastpowdercoating.com/innovative-powder-coating-trends
[8] https://www.paint.org/coatingstech-magazine/articles/new-advances-in-powder-coating-technology/
[9] http://www.ieecon.org/blog/innovations-in-metal-powder-press-tech/
[10] https://www.chinapowdercoating.com/emerging-technologies-shaping-the-future-of-powder-coatings/
---
Hot Tags: China, Global, OEM, private label, manufacturers, factory, suppliers, manufacturing company