Content Menu
● Understanding Electrostatic Spray Guns
>> What is an Electrostatic Spray Gun?
>> How Electrostatic Spray Guns Work
>> Types of Electrostatic Spray Guns
● Components of an Electrostatic Spray Gun System
>> The Spray Gun
>> Power Supply and Control System
>> Fluid and Air Delivery
● Advantages of Electrostatic Spray Guns
>> High Transfer Efficiency
>> Improved Finish Quality
>> Environmental Benefits
>> Increased Production Throughput
● Electrostatic Spray Gun Control Systems
>> Purpose and Functionality
>> Features of Modern Control Systems
>> Integration with Automation
● Manufacturing Electrostatic Spray Guns and Control Systems
>> Factory Setup and Production Process
>> Quality Assurance
>> Innovation and Development
● Applications of Electrostatic Spray Guns
>> Automotive Industry
>> Aerospace
>> Furniture and Metal Fabrication
>> Food Safety and Agriculture
● Maintenance and Troubleshooting
>> Routine Maintenance
>> Common Issues
>> Factory Support
● Future Trends in Electrostatic Spray Technology
>> Smart Control Systems
>> Eco-Friendly Coatings
>> Enhanced Ergonomics
● Frequently Asked Questions
● Citations:
Electrostatic spray guns and their control systems have revolutionized the coating and finishing industries by providing efficient, high-quality, and environmentally friendly solutions for applying paints, powders, and other coatings. This article explores the technology behind electrostatic spray guns, the design and operation of control systems, the benefits of using these systems in manufacturing, and the role of factories specializing in their production.
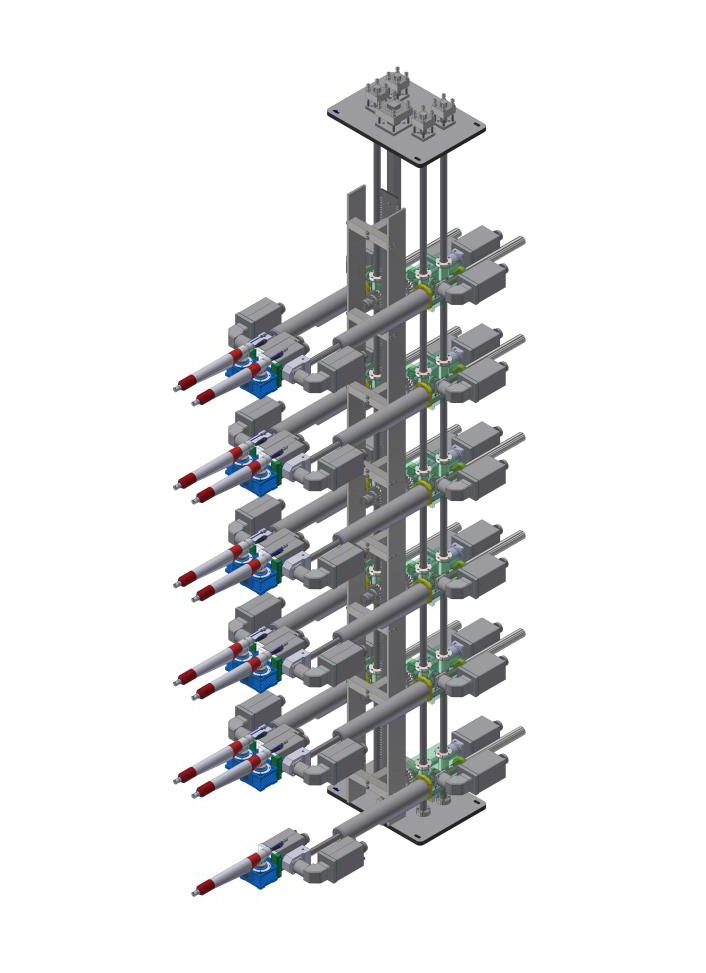
Understanding Electrostatic Spray Guns
What is an Electrostatic Spray Gun?
An electrostatic spray gun is a device that applies paint or powder coatings by electrically charging the particles as they exit the gun. The charged particles are attracted to the grounded workpiece, resulting in a more uniform and efficient coating. This process significantly reduces overspray and waste, improving transfer efficiency and finish quality.
How Electrostatic Spray Guns Work
The core principle involves charging the coating material (liquid or powder) with a high-voltage electrostatic charge, typically up to 90 kV or more. As the atomized particles leave the gun, they carry this charge and are attracted to the oppositely charged or grounded target surface. This attraction causes the particles to wrap around the object, even reaching recesses and complex shapes, ensuring thorough coverage.
Types of Electrostatic Spray Guns
- Manual Electrostatic Spray Guns: Operated by hand, these guns are versatile and suitable for small to medium production runs or touch-up work.
- Automatic Electrostatic Spray Guns: Integrated into robotic or automated systems for high-volume, consistent coating applications.
- Rotary Bell Electrostatic Guns: Use a rotating bell to atomize the coating, providing ultra-fine particles and high transfer efficiency, ideal for intricate parts.
Components of an Electrostatic Spray Gun System
The Spray Gun
The spray gun includes the fluid delivery system, atomizing air or powder feed, and the electrostatic charging mechanism. Modern guns feature ergonomic designs for operator comfort and durability to withstand industrial environments.
Power Supply and Control System
The power supply generates the high voltage needed to charge the coating particles. The control system regulates voltage, current, and other parameters to optimize coating quality and safety. Advanced systems offer automatic current limiting and adjustable voltage to suit different coatings and part geometries.
Fluid and Air Delivery
For liquid coatings, precise fluid tips and air caps control the atomization pattern and flow rate. For powder coatings, the system controls powder feed rate and electrostatic charge to ensure consistent application.
Advantages of Electrostatic Spray Guns
High Transfer Efficiency
Electrostatic spray guns can achieve transfer efficiencies of up to 95%, meaning most of the coating material adheres to the part, reducing waste and material costs.
Improved Finish Quality
The electrostatic charge causes the coating to wrap around parts, providing uniform coverage, smooth finishes, and better adhesion, even on complex shapes.
Environmental Benefits
Reduced overspray lowers volatile organic compound (VOC) emissions and hazardous air pollutants (HAPs), making electrostatic spraying an environmentally responsible choice.
Increased Production Throughput
Faster application and less rework due to improved finish quality increase overall production efficiency.
Electrostatic Spray Gun Control Systems
Purpose and Functionality
Control systems manage the electrical parameters and fluid delivery to maintain consistent coating quality. They ensure operator safety by monitoring current and voltage and provide diagnostics to minimize downtime.
Features of Modern Control Systems
- Automatic Current Limiting: Adjusts the charge to prevent arcing and optimize coverage.
- User Interface: Touchscreens or digital displays for easy parameter adjustments.
- Safety Interlocks: Prevent operation under unsafe conditions.
- Data Logging: Records operational data for quality control and maintenance.
Integration with Automation
Control systems can be integrated with robotic arms and conveyor systems for fully automated coating lines, enhancing repeatability and reducing labor costs.
Manufacturing Electrostatic Spray Guns and Control Systems
Factory Setup and Production Process
Factories specializing in electrostatic spray guns and control systems combine precision engineering, electronics manufacturing, and quality control. Key production steps include:
- Component Fabrication: Machining of gun bodies, nozzles, and electrical components.
- Assembly: Integration of fluid delivery, charging electrodes, and control electronics.
- Testing: Electrical safety, coating performance, and durability tests.
- Calibration: Adjusting control systems for optimal performance with various coatings.
Quality Assurance
Strict quality control ensures each unit meets industry standards for safety, efficiency, and durability. Factories often hold certifications such as ISO to guarantee consistent product quality.
Innovation and Development
Continuous R&D efforts focus on improving transfer efficiency, reducing maintenance, and enhancing user ergonomics. Feedback from factory users helps refine designs for durability and performance.
Applications of Electrostatic Spray Guns
Automotive Industry
Used extensively for painting car bodies and parts, electrostatic spray guns provide high-quality finishes with minimal waste.
Aerospace
Precision coating of aircraft components requires the fine atomization and wrap-around effect of electrostatic spraying.
Furniture and Metal Fabrication
Electrostatic powder coating guns are popular for finishing metal furniture, fences, and architectural profiles.
Food Safety and Agriculture
Electrostatic sprayers are used for disinfecting surfaces and applying treatments in agriculture, ensuring thorough coverage with minimal chemical use.
Maintenance and Troubleshooting
Routine Maintenance
Regular cleaning of fluid passages, inspection of electrodes, and checking electrical connections are essential to maintain performance.
Common Issues
- Arcing: Caused by improper grounding or excessive voltage.
- Poor Atomization: Due to clogged nozzles or incorrect air pressure.
- Inconsistent Coating: May result from faulty control system settings or worn components.
Factory Support
Manufacturers provide technical support, spare parts, and training to ensure optimal operation and quick resolution of issues.
Future Trends in Electrostatic Spray Technology
Smart Control Systems
Integration of IoT and AI for predictive maintenance and real-time process optimization.
Eco-Friendly Coatings
Development of waterborne and low-VOC coatings compatible with electrostatic application.
Enhanced Ergonomics
Lighter, more comfortable guns with improved user interfaces to reduce operator fatigue.
---
Frequently Asked Questions
Q1: What materials can be applied using electrostatic spray guns?
A1: Electrostatic spray guns can apply a variety of materials including liquid paints, powder coatings, and specialty coatings like waterborne paints.
Q2: How does electrostatic spraying reduce paint waste?
A2: The charged particles are attracted to the grounded part, resulting in more paint adhering to the surface and less overspray, which reduces waste.
Q3: Are electrostatic spray guns safe to use?
A3: Yes, modern systems include safety features such as automatic current limiting and grounding checks to prevent electrical hazards.
Q4: Can electrostatic spray guns be used on non-metallic surfaces?
A4: While most effective on conductive surfaces, some systems can coat non-metallic parts by using conductive primers or specialized techniques.
Q5: What maintenance is required for electrostatic spray guns?
A5: Regular cleaning of nozzles, inspection of electrodes, and checking electrical connections are necessary to maintain optimal performance.
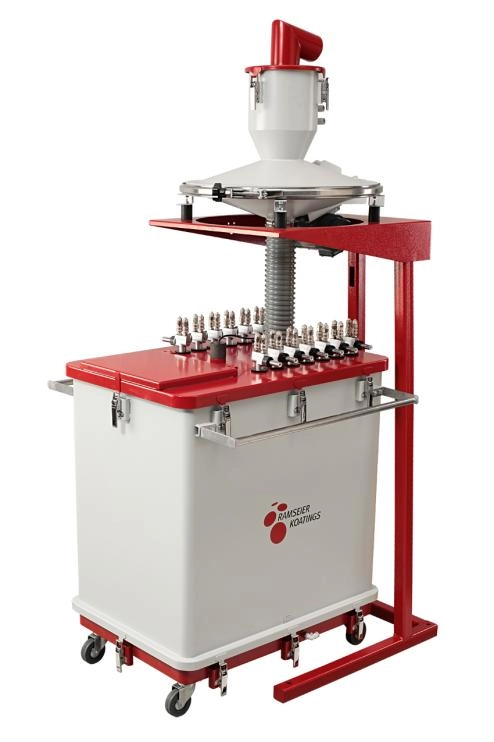
---
Citations:
[1] https://www.graco.com/us/en/in-plant-manufacturing/products/liquid-coating/spray-booth/spray-guns-applicators/electrostatic-paint-spray-guns.html
[2] https://maxcharge.com
[3] https://www.nordson.com/en/products/industrial-coating-systems-products/trilogy-electrostatic---spray-systems
[4] https://www.graco.com/us/en/in-plant-manufacturing/solutions/articles/electrostatic-spray-gun-basics.html
[5] https://carlisleft.com/product/ransburg-no-2-gun/
[6] https://patents.google.com/patent/CN1727835A/zh
[7] https://www.joboncoating.com/electrostatic-powder-coating-machine/electrostatic-powder-coating-gun-and-control.html
[8] https://patents.google.com/patent/CN110665668A/zh
---
Hot Tags: China, Global, OEM, private label, manufacturers, factory, suppliers, manufacturing company