Content Menu
● Introduction
● Understanding the Fundamentals
>> What is a Spray Gun Unit?
>> What is Traditional Liquid Painting?
● Comparative Analysis: Speed, Efficiency, and Finish Quality
>> Production Speed
>>> Spray Gun Unit
>>> Traditional Liquid Painting
>> Finish Quality and Consistency
>>> Spray Gun Unit
>>> Traditional Liquid Painting
>> Material Efficiency and Waste
>>> Spray Gun Unit
>>> Traditional Liquid Painting
>> Labor and Ergonomics
>>> Spray Gun Unit
>>> Traditional Liquid Painting
>> Cost Considerations
>>> Initial Investment
>>> Operating Costs
● Efficiency and Scalability on the Production Line
>> Throughput and Volume
>> Maintenance and Downtime
● Environmental and Safety Considerations
>> Spray Gun Unit
>> Traditional Liquid Painting
>> Compliance
● Suitability for Different Production Needs
>> When to Choose Spray Gun Units
>> When to Choose Traditional Liquid Painting
● Case Studies and Real-World Insights
>> Industrial Success with Spray Guns
>> Brush and Roller Preference in Artisanal Production
● Long-Term Cost Analysis
>> Life Cycle Costs
>> Consumable Costs
● Skill, Training, and Operator Requirements
● Innovation and Future Trends
● Pros and Cons Summary Table
● Frequently Asked Questions (FAQs)
>> 1. Which method delivers a better surface finish?
>> 2. Are spray gun units more cost-effective for high-volume production?
>> 3. Is traditional liquid painting obsolete for industrial use?
>> 4. What environmental precautions are necessary for spray gun systems?
>> 5. Can both methods be combined on a single production line?
Introduction
In the manufacturing sector, the finishing process is critical for product appearance, durability, and value. Two primary painting methods dominate: the modern spray gun unit and traditional liquid painting (brush and roller applications). Choosing the right method for your production line impacts everything from efficiency and cost to environmental compliance and worker health. This comprehensive analysis examines both solutions, detailing their advantages, drawbacks, operational requirements, and provides guidance to help you select the optimal approach for your production needs.
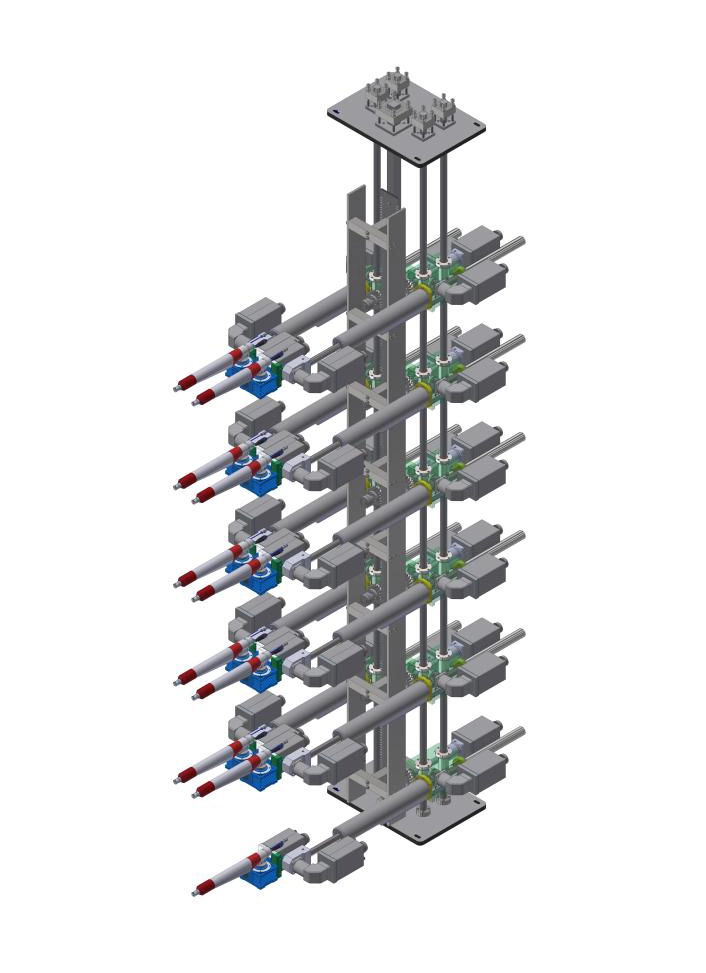
Understanding the Fundamentals
What is a Spray Gun Unit?
A spray gun unit is a mechanical tool that atomizes paint into fine droplets, enabling fast, uniform application across surfaces. Driven by compressed air or high-pressure systems, spray guns are widely used in automotive, furniture, industrial, and construction sectors for their consistent finish and speed.
Key Features of Spray Gun Units:
- Delivers even coats on complex and flat surfaces
- Enables quick coverage of large areas
- Offers multiple nozzle types for variable textures and finishes
- Can utilize various paint formulations (oil, water-based, lacquer, etc.)
What is Traditional Liquid Painting?
Traditional liquid painting relies on manual tools—such as brushes and rollers—to apply paint directly to surfaces. This method has been the industry standard for centuries, prized for its control and craftsmanship in small, intricate, or touch-up work.
Key Features of Traditional Liquid Painting:
- Ensures meticulous precision in detailed or confined areas
- Suitable for small-batch, custom, or repair work
- Flexible with a wide range of brush and roller sizes
Comparative Analysis: Speed, Efficiency, and Finish Quality
Production Speed
Spray Gun Unit
Spray gun units excel in application speed, enabling operators to paint large areas in a fraction of the time compared to manual methods. This speed translates to increased throughput on busy production lines, crucial for high-volume manufacturing or tight deadlines.
Traditional Liquid Painting
Traditional methods are slower due to manual application pace and the potential need for multiple coats. Drying times may lengthen due to thicker or less-uniform coats, which can stall subsequent manufacturing steps.
Summary Table: Application Speed
Method | Application Speed | Scalability |
Spray Gun Unit | Fast | High |
Traditional Liquid Painting | Slow | Low–Medium |
Finish Quality and Consistency
Spray Gun Unit
Spray guns are renowned for delivering a smooth, uniform finish with minimized brush marks or uneven streaks. The atomization process allows paint to settle evenly on both simple and complex geometries—ideal for products where appearance is vital.
Traditional Liquid Painting
Manual methods can produce high-quality results, especially for detailed work, but risk visible brush strokes, roller marks, or uneven coverage—especially over large or textured surfaces. Achieving consistent results across many units requires significant operator skill and attention.
Material Efficiency and Waste
Spray Gun Unit
Modern spray gun units (especially HVLP, LVLP, or electrostatic models) offer efficient transfer rates, reducing overspray and minimizing wasted paint. Some premium guns approach transfer efficiencies up to 65% or higher, lessening both cost and environmental footprint.
However, if not properly calibrated or used by untrained operators, spray guns can still generate material waste via overspray.
Traditional Liquid Painting
Painting with brushes or rollers minimizes waste on targeted zones, making it ideal for small batches, touch-ups, or confined areas. However, unskilled application can lead to over-application, drips, or uneven surfaces.
Material Waste Comparison:
- Spray Gun Unit: Moderate (lower with experience and correct equipment)
- Traditional: Low for small tasks, higher risk in larger areas due to uneven application
Labor and Ergonomics
Spray Gun Unit
Operators benefit from reduced physical fatigue, as spray guns require less repetitive motion than brushing or rolling. Ergonomically designed units lessen strain on wrists, shoulders, and backs, especially on long production runs. Additionally, automation is easier to implement with spray technology, reducing labor dependence.
Traditional Liquid Painting
Manual painting is labor-intensive, especially over large areas, textured surfaces, or multi-coat applications. Operator fatigue is a real concern, limiting daily productivity and increasing the likelihood of repetitive strain injuries.
Cost Considerations
Initial Investment
- Spray Gun Units: Typically require higher up-front capital for equipment, booths, compressors, and safety gear, especially when scaling up.
- Traditional Liquid Painting: Lower initial costs for tools, but escalating labor costs and lower throughput on large projects.
Operating Costs
- Spray Gun Units: Use less labor per unit, less paint thanks to higher transfer efficiency, and often require less rework. Maintenance and spare parts must be factored in.
- Traditional Liquid Painting: Low consumable cost but high ongoing labor expenses for large volumes, with possible cost increases due to slower turnaround and potential for rework.
Efficiency and Scalability on the Production Line
Throughput and Volume
- Spray Gun Units can be integrated into automated lines, supporting high-volume, repetitive production.
- Traditional Liquid Painting is best suited to low-volume, bespoke, or intricate work, where flexibility and precision matter more than speed.
Maintenance and Downtime
- Spray Gun Units need regular cleaning, inspection, and occasional spare parts or calibration—scheduled maintenance can help avoid unplanned downtime.
- Traditional Liquid Painting tools are simple, require less technical maintenance, but changeovers (e.g., between colors or formulations) are time-consuming and prone to error.
Environmental and Safety Considerations
Spray Gun Unit
- Generates more airborne particles (overspray/vapors) requiring robust ventilation, filtration, and sometimes dedicated spray booths
- High-quality spray gun models can reduce overspray and volatile organic compound (VOC) emissions
- Some systems support water-based paints, further mitigating environmental risks
Traditional Liquid Painting
- Manual methods generate less airborne material but still emit VOCs if solvent-heavy paints are used
- Safer in environments without advanced ventilation
Compliance
Both methods must adhere to increasingly strict environmental regulations. Automated spray lines with modern filtration are more likely to meet compliance in high-volume operations.
Suitability for Different Production Needs
When to Choose Spray Gun Units
- Large-scale, repetitive manufacturing
- Need for rapid turnaround
- Uniform, professional finish is essential
- Parts with complex shapes or hard-to-reach recesses
- Plans to scale or automate production
When to Choose Traditional Liquid Painting
- Small volume or highly customized production
- Repair, rework, or touch-up scenarios
- Tight budget for initial capital outlay
- Maximum precision on detailed features
Case Studies and Real-World Insights
Industrial Success with Spray Guns
A plastics manufacturing firm replaced traditional HVLP spray guns with ergonomically-designed models, cutting material use by one-third, reducing worker fatigue, and decreasing reject rates dramatically while raising overall daily throughput.
Brush and Roller Preference in Artisanal Production
Custom furniture makers and fine finishers often prefer traditional methods for their unmatched control on fine details, achieving nuanced textures and hues that spraying may not replicate.
Long-Term Cost Analysis
Life Cycle Costs
- Spray Gun Units are more expensive initially but pay for themselves through labor savings, reduced waste, fewer rejects, and productivity gains.
- Traditional Liquid Painting is best when scaling up is not the goal—its operating costs mount over time due to labor intensity.
Consumable Costs
Spray systems may require occasional replacements (nozzles, filters, needles), but allow for long-lasting, repairable equipment. Premium guns can often be rebuilt instead of discarded, reducing long-term waste.
Skill, Training, and Operator Requirements
- Spray Gun Operators need training in calibration, safety protocols, and surface preparation. Mastery delivers high returns in efficiency and finish quality.
- Traditional Painters require dexterity and experience, especially with detailed or intricate work, but may not need technical training on complex equipment.
Innovation and Future Trends
The industry is moving toward more automated, efficient, and eco-friendly solutions. Emerging spray gun technologies focus on maximizing transfer efficiency, minimizing waste, and integrating IoT sensors for QA tracking. Traditional painting, while less common in mass production, remains essential for artistic, small-batch, or high-customization settings.
Pros and Cons Summary Table
Aspect | Spray Gun Unit | Traditional Liquid Painting |
Application Speed | Fast, consistent | Slow, highly variable |
Finish Quality | Uniform, professional | Prone to marks/streaks |
Material Efficiency | High with experience/equipment | High for small jobs, low on large |
Environmental Control | Needs ventilation/booth | Simpler control, less airborne |
Operator Skill | Requires technical training | Requires manual skill |
Initial Cost | High | Low |
Long-term Cost | Lower due to efficiency | High labor, slower throughput |
Scalability | Easy to automate/scale | Hard to scale, best for one-offs |
Maintenance | Regular cleaning/repairs | Minimal, but slow tool changeover |
Frequently Asked Questions (FAQs)
1. Which method delivers a better surface finish?
Spray gun units typically provide a smoother, more uniform finish without brush marks or roller stippling. Manual methods can yield excellent results for detailed work but are less consistent across large or complex parts.
2. Are spray gun units more cost-effective for high-volume production?
Yes. While the up-front investment is greater, spray gun units improve efficiency, reduce labor, minimize material waste, and accelerate throughput, resulting in significant long-term savings.
3. Is traditional liquid painting obsolete for industrial use?
No. Traditional painting excels in specialized, small-batch, or detail-driven contexts. It's essential for areas requiring precision or custom finishes.
4. What environmental precautions are necessary for spray gun systems?
Spray operations must utilize proper ventilation, filtration systems, and personal protective equipment to protect workers and ensure regulatory compliance, especially when using solvent-based formulations.
5. Can both methods be combined on a single production line?
Yes. Many factories use spray guns for primary coverage and traditional methods for touch-ups, intricate detailing, or repairs, leveraging the strengths of both techniques.
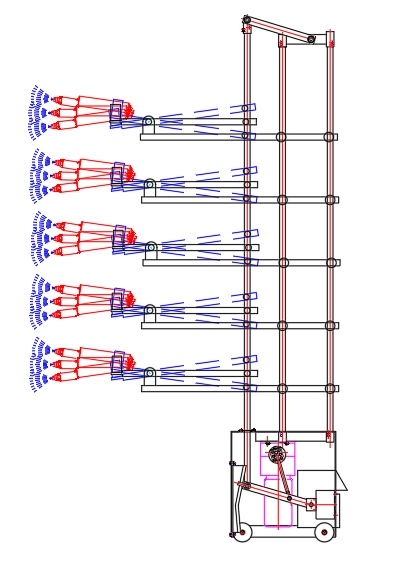
[1] https://www.formula.co.nz/page/9/benefits-of-using-a-spray-gun
[2] https://www.codinter.com/en/electrostatic-vs-conventional-painting-which-process-is-better/
[3] https://www.pfonline.com/articles/service-plastics-improves-bottom-line
[4] https://www.sarcoatings.com/blog/liquid-painting-vs-spray-painting-understanding-the-differences/
[5] https://pittsburghsprayequip.com/blogs/pittsburgh-spray-equipment-company/how-much-does-a-paint-gun-cost-a-complete-guide-based-on-different-gun-types
[6] https://www.airblasteurospraydirect.com/blog/what-are-the-pros-and-cons-of-using-a-paint-sprayer/
[7] https://www.crestcoating.com/cci-blog/powder-coating-vs-liquid-painting-a-comprehensive-comparison/
[8] https://pittsburghsprayequip.com/blogs/pittsburgh-spray-equipment-company/when-to-use-conventional-spray-guns-vs-airless-paint-sprayers
[9] https://www.youtube.com/watch?v=KSd1RknEgm0
[10] https://www.graco.com/us/en/in-plant-manufacturing/solutions/articles/take-the-paint-efficiency-audit.html
[11] https://www.wagner-group.com/en/do-it-yourself/companion/why-its-better-to-spray/
[12] https://tritechindustries.com/airless-sprayers-vs-traditional-methods/
[13] https://www.graco.com/us/en/in-plant-manufacturing/solutions/articles/conventional-vs-electrostatic-spray-guns.html
[14] https://www.reddit.com/r/Autobody/comments/151q65p/fluid_control_vs_needle_size_spray_painting/
[15] https://www.ramseierkoatings.com/electrostatic-spray-gun-vs-hvlp-which-is-more-cost-effective.html
[16] https://navite.com/spray-guns-vs-brushing-and-rolling-weighing-the-advantages-and-disadvantages-of-painting-methods/
[17] https://coatingchic.com/comparing-powder-coating-to-traditional-paint-pros-and-cons/
[18] https://www.bolair.ca/blog/comparative-analysis-spray-guns/
[19] https://www.youtube.com/watch?v=ubeAS80Nrzg
[20] https://martinsupply.com/case-study/integrated-paint-gun/
Hot Tags: China, Global, OEM, private label, manufacturers, factory, suppliers, manufacturing company