Introduction to Powder Center and Hoppers
As a leading innovator in powder coating solutions, our company has been at the forefront of designing and manufacturing top-tier powder center and hoppers for over 38 years. These critical components are integral to our comprehensive powder coating systems, ensuring efficient and precise powder management. In this article, we will delve into the world of powder center and hoppers, exploring their definition, market trends, manufacturing process, types, and maintenance requirements.
What are Powder Center and Hoppers?
Powder center and hoppers are specialized systems designed to manage and distribute powder materials effectively. The powder center acts as a hub, integrating various components such as powder hoppers, fluidization systems, and control mechanisms to ensure consistent powder flow. Powder hoppers, on the other hand, are containers that store and dispense powder materials, often equipped with mechanisms like vibration or pneumatic systems to facilitate smooth powder flow. These systems are crucial in industries requiring precise powder coating, such as automotive and aerospace.
The powder center ensures that powder is evenly distributed to multiple coating stations, while powder hoppers can be customized to handle different types of powders, from fine powders to granular materials. This flexibility makes powder center and hoppers essential for a wide range of applications, from small-scale operations to large industrial settings.
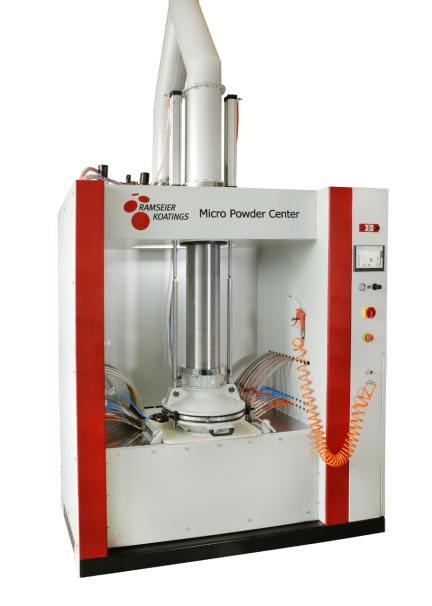
Market of Powder Center and Hoppers
The market for powder center and hoppers is growing rapidly, driven by increasing demand from industries such as automotive, aerospace, and consumer goods. This growth is fueled by the need for efficient, high-quality powder coating processes that can meet stringent production standards. Technological advancements in powder center and hoppers, such as automation and IoT integration, have further enhanced their appeal by improving productivity and reducing operational costs.
In recent years, there has been a significant shift towards more sustainable and environmentally friendly coating solutions, with powder center and hoppers playing a key role in minimizing waste and optimizing powder usage. As industries continue to evolve, the demand for advanced powder center and hoppers that can integrate seamlessly with existing systems while offering superior performance is expected to rise.
How to Make Powder Center and Hoppers
Manufacturing powder center and hoppers involves a combination of precision engineering and material selection. The process typically includes:
1. Design and Prototyping: Creating detailed designs that meet specific application requirements, including material flow rates and powder types. This stage is critical in ensuring that the final product meets the needs of various industries, from food processing to pharmaceuticals.
2. Material Selection: Choosing durable materials such as stainless steel or aluminum to ensure longevity and resistance to corrosion. These materials are often used in powder hoppers to prevent contamination and ensure smooth powder flow.
3. Fabrication: Constructing the powder hoppers and integrating them with fluidization systems and control units. This step requires careful attention to detail to ensure that all components work harmoniously to provide consistent powder delivery.
4. Testing and Quality Control: Ensuring that the final product meets performance and safety standards. This includes testing the fluidization systems, powder flow rates, and ensuring that all components are properly grounded to prevent static electricity issues.
Types of Powder Center and Hoppers
There are several types of powder center and hoppers available, each tailored to specific needs:
- Fluidized Hoppers: These use compressed air to fluidize the powder, ensuring smooth flow and preventing clogging. They are ideal for handling fine powders and are commonly used in industries such as ceramics and pharmaceuticals.
- Vibratory Hoppers: Equipped with vibrating mechanisms to facilitate powder flow, ideal for materials that tend to compact. These are often used in applications where powders are prone to settling or caking.
- Pneumatic Conveying Systems: Utilize air pressure to transport powder from the hopper to the application point. This method is efficient for long-distance powder transport and is commonly used in large-scale industrial settings.
- Modular Powder Centers: Designed for flexibility, allowing easy integration with various powder coating systems. These modular systems are ideal for operations that require frequent color changes or adjustments in powder flow rates.
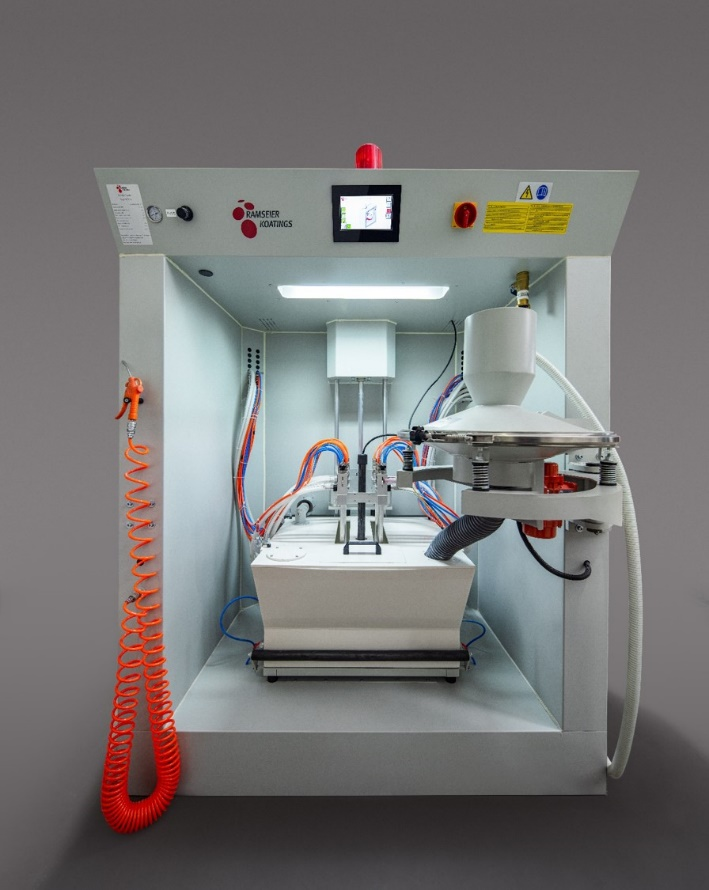
Applications of Powder Center and Hoppers
Powder center and hoppers are widely used across various industries due to their versatility and efficiency:
- Automotive Industry: Used for coating car parts, ensuring durable and high-quality finishes.
- Aerospace Industry: Essential for applying specialized coatings to aircraft components, requiring precise control over powder application.
- Food Processing: Though less common, powder hoppers can be adapted for handling food-grade powders, ensuring cleanliness and precision in packaging processes.
- Pharmaceutical Industry: Used in the formulation and packaging of pharmaceutical powders, where accuracy and purity are paramount.
Maintenance of Powder Center and Hoppers
Regular maintenance is crucial to extend the lifespan of powder center and hoppers and maintain optimal performance:
1. Cleaning: Regularly clean the interior and exterior of powder hoppers to prevent powder buildup and contamination. This includes using industrial vacuum cleaners and soft brushes to remove powder residues without damaging the fluidizing plates.
2. Inspection: Check for wear and tear on moving parts and fluidization systems. Ensure that all components are properly secured and functioning as intended.
3. Replacement of Worn Parts: Replace components like membranes or vibrating mechanisms as needed. This prevents downtime and ensures consistent powder flow.
4. Grounding and Safety Checks: Ensure proper grounding to prevent static electricity issues and maintain safety standards. This includes wearing appropriate protective gear during maintenance to avoid respiratory and eye irritation from powder dust.
5. Disassembly and Reassembly: Powder hoppers should be designed for easy disassembly and reassembly, facilitating thorough cleaning and maintenance without tools. This feature is essential for industries requiring frequent product changeovers or sanitation measures.
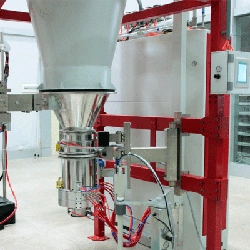
In conclusion, powder center and hoppers are vital components in modern powder coating systems, offering precision, efficiency, and reliability. By understanding their design, manufacturing process, types, and maintenance needs, industries can optimize their powder coating processes to achieve superior quality and productivity. Our company remains committed to innovating and improving powder center and hoppers to meet the evolving demands of the global market.
Come and contact us to shop! ! !