Content Menu
● Introduction to Spray Technologies
>> Conventional Spray Systems
>> Automatic Electrostatic Spray Guns
● How Automatic Electrostatic Spray Guns Work
>> The Electrostatic Charging Process
>> Wraparound Effect
>> Droplet Size and Atomization
● Key Differences Between Automatic Electrostatic and Conventional Spray Systems
● Advantages of Automatic Electrostatic Spray Guns
>> Superior Finish Quality
>> Increased Transfer Efficiency
>> Reduced Overspray and Environmental Benefits
>> Cost Savings Over Time
>> Safer and Healthier Work Environment
● Limitations and Challenges of Electrostatic Spray Guns
>> The Faraday Cage Effect
>> Material Compatibility
>> Equipment Complexity and Maintenance
● Applications of Automatic Electrostatic Spray Guns
>> Industrial Coating and Painting
>> Disinfection and Sanitization
>> Agricultural and Pest Control
>> Consumer Products and Furniture
● How to Choose Between Electrostatic and Conventional Spray Systems
● Conclusion
● Frequently Asked Questions
Spray painting and coating technologies have evolved significantly over the years, with automatic electrostatic spray guns emerging as a powerful alternative to conventional spray systems. Understanding the differences between these two technologies is crucial for industries aiming to improve coating quality, reduce costs, and minimize environmental impact. This article explores the fundamental distinctions, advantages, limitations, and applications of automatic electrostatic spray guns compared to conventional spray systems.
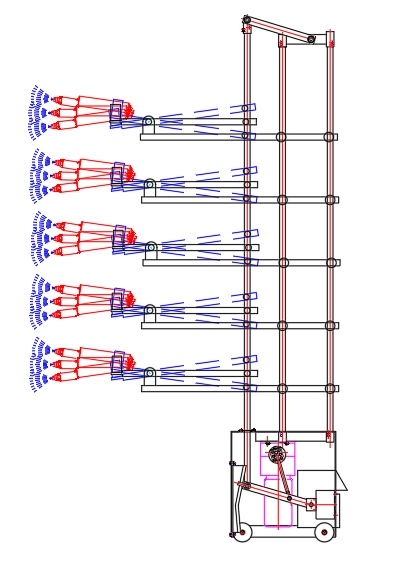
Introduction to Spray Technologies
Spray systems are widely used in various industries such as automotive, manufacturing, agriculture, and healthcare for applying paints, coatings, disinfectants, and other fluids. The choice of spray technology affects the efficiency, quality, and environmental footprint of the coating process.
Conventional Spray Systems
Conventional spray guns operate by atomizing paint or coating material using compressed air to create a spray pattern. The droplets are propelled towards the target surface, relying primarily on the momentum of the air stream to deposit the material. While effective, this method often results in significant overspray, waste of materials, and uneven coverage, especially on complex shapes.
Automatic Electrostatic Spray Guns
Automatic electrostatic spray guns add an electrical charge to the paint or coating particles as they exit the spray nozzle. These charged particles are attracted to the grounded target surface, resulting in a phenomenon known as "wraparound," where the coating covers not only the front but also the undersides and backsides of objects. This technology is typically integrated into automated systems for consistent and efficient application.
How Automatic Electrostatic Spray Guns Work
The Electrostatic Charging Process
In an electrostatic spray gun, the coating material passes through a charging zone where it receives a negative electrical charge. The target object is grounded or positively charged, creating an electrostatic field that attracts the negatively charged droplets. This attraction forces the droplets to move toward the surface with a force much stronger than gravity, enhancing deposition efficiency.
Wraparound Effect
Unlike conventional spray guns that coat only the surface directly in front of the nozzle, electrostatic spray guns enable the coating particles to "wrap around" the object. This effect ensures coverage of hard-to-reach areas, such as the backside of tubular components, leading to a more uniform and complete finish.
Droplet Size and Atomization
Electrostatic systems produce significantly smaller droplets — up to 900 times smaller than those from conventional sprayers. Smaller droplets improve coverage uniformity and reduce the amount of coating material needed. The atomization process in electrostatic guns is similar to that of High Volume Low Pressure (HVLP) guns but enhanced by the electrical charge that separates particles and reduces forward velocity, improving transfer efficiency.
Key Differences Between Automatic Electrostatic and Conventional Spray Systems
Feature | Conventional Spray Systems | Automatic Electrostatic Spray Guns |
Droplet Size | Larger droplets, less uniform coverage | Much smaller droplets, highly uniform coverage |
Transfer Efficiency | Low (around 25%) with high overspray | High (up to 95%) with minimal overspray |
Coverage | Only surfaces directly in front of the nozzle | Wraparound coverage including undersides and backsides |
Material Waste | High due to overspray and bounce-back | Significantly reduced, saving material costs |
Environmental Impact | Higher VOC emissions and chemical waste | Lower VOC emissions and reduced environmental load |
Equipment Cost | Lower initial cost | Higher initial cost but rapid ROI due to efficiency |
Suitability for Complex Shapes | Limited coverage on complex geometries | Excellent coverage, except in deep recessed areas due to Faraday cage effect |
Advantages of Automatic Electrostatic Spray Guns
Superior Finish Quality
Electrostatic spray guns deliver an excellent finish quality by ensuring even coating thickness and smooth surface texture. The wraparound effect eliminates missed spots and reduces the need for rework.
Increased Transfer Efficiency
With transfer efficiency reaching up to 95%, electrostatic spraying minimizes paint or coating loss. This efficiency reduces material consumption and lowers operational costs significantly.
Reduced Overspray and Environmental Benefits
Because the charged particles are attracted to the target, less material escapes into the air as overspray. This reduction decreases volatile organic compound (VOC) emissions, improving air quality and worker safety.
Cost Savings Over Time
Although electrostatic spray systems have a higher upfront cost, the savings from reduced material use, less cleanup, and faster production cycles provide a strong return on investment.
Safer and Healthier Work Environment
Lower chemical exposure due to reduced overspray makes electrostatic spraying safer for operators and others in the vicinity, such as students in educational settings or workers in industrial plants.
Limitations and Challenges of Electrostatic Spray Guns
The Faraday Cage Effect
One notable limitation is the Faraday cage effect, where charged particles tend to coat the edges of recessed or deeply contoured areas rather than penetrating into them. This can result in uneven coating in corners or cavities.
Material Compatibility
Electrostatic spraying works best with conductive or semi-conductive materials. Non-conductive substrates like plastic or wood may require a conductive primer to optimize coating adhesion.
Equipment Complexity and Maintenance
Electrostatic systems are more complex and require careful maintenance to ensure consistent charging and spray quality. Operators may need specialized training to handle the equipment safely and effectively.
Applications of Automatic Electrostatic Spray Guns
Industrial Coating and Painting
Electrostatic spray guns are widely used in automotive manufacturing, metal fabrication, and appliance production where high-quality finishes and efficient material use are critical.
Disinfection and Sanitization
During health crises such as pandemics, electrostatic sprayers have been employed to apply disinfectants evenly and quickly over large areas, improving sanitation effectiveness while reducing chemical use.
Agricultural and Pest Control
Electrostatic technology enhances the application of pesticides and nutrients by ensuring better coverage on plant surfaces, reducing chemical waste and environmental contamination.
Consumer Products and Furniture
For items like tubular furniture, electrostatic spray guns provide superior coverage and finish quality, especially on complex shapes that are difficult to coat uniformly with conventional methods.
How to Choose Between Electrostatic and Conventional Spray Systems
When deciding which spray system to use, consider the following factors:
- Surface Geometry: Electrostatic spraying excels on complex shapes but may struggle with deep recesses.
- Material Costs: High material costs favor electrostatic spraying due to better transfer efficiency.
- Production Volume: Automated electrostatic systems are ideal for high-volume production with consistent quality requirements.
- Budget: Conventional systems have lower upfront costs but higher ongoing material and labor expenses.
- Environmental Regulations: Electrostatic spraying reduces VOC emissions and overspray, helping meet stricter environmental standards.
Conclusion
Automatic electrostatic spray guns represent a significant advancement over conventional spray systems by combining electrical charge technology with precision atomization to achieve superior coating quality, material savings, and environmental benefits. While they require a higher initial investment and have some limitations like the Faraday cage effect, their advantages in efficiency and finish quality make them the preferred choice in many industrial and commercial applications.
Frequently Asked Questions
1. What is the main advantage of an automatic electrostatic spray gun over a conventional spray system?
The main advantage is the electrostatic charge that causes paint particles to be attracted to the target surface, resulting in higher transfer efficiency, less overspray, and wraparound coverage.
2. Can electrostatic spray guns be used on non-conductive materials?
Yes, but often a conductive primer is required to optimize the electrostatic effect on non-conductive substrates like plastic or wood.
3. What is the Faraday cage effect in electrostatic spraying?
It is a phenomenon where charged particles coat the edges of recessed areas rather than penetrating into them, causing uneven coverage in deep corners.
4. Are electrostatic spray guns more expensive than conventional spray guns?
Yes, electrostatic systems have a higher initial cost but offer savings over time through reduced material use and improved efficiency.
5. How does electrostatic spraying impact environmental safety?
It reduces overspray and VOC emissions, lowering chemical waste and improving air quality for workers and surrounding environments.
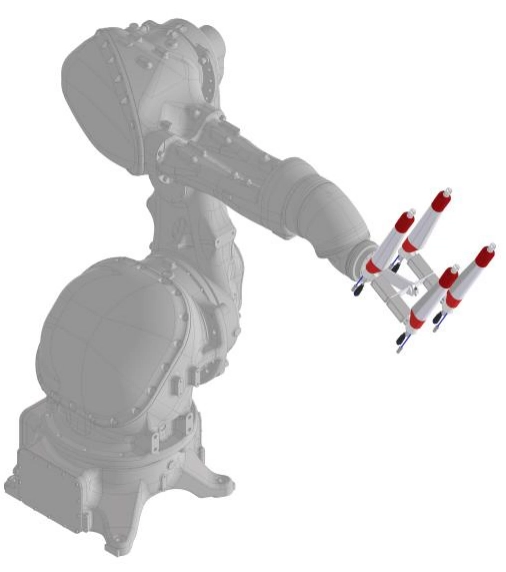
[1] https://fortcollinschamber.com/wp-content/uploads/2020/04/The-Difference-Between-Electrostatic-Sprayers-vs-Conventional-Sprayers-2-1.pdf
[2] https://www.scribd.com/document/10317685/%E5%A4%A7%E5%AD%A6%E7%A7%91%E6%8A%80%E8%8B%B1%E8%AF%AD
[3] https://www.decc.com/recent-articles/hvlp-spray-vs-electrostatic-spray/
[4] https://www.graco.com/us/en/in-plant-manufacturing/solutions/articles/conventional-vs-electrostatic-spray-guns.html
[5] https://www.cetinc.com/should-i-be-using-electrostatic-spray/
[6] https://elmbridgeuk.com/learning-hub/7-reasons-to-use-an-electrostatic-spray-gun/
[7] https://www.graco.com/us/en/in-plant-manufacturing/solutions/articles/advantages-of-spraying-with-electrostatic-guns.html
[8] https://www.codinter.com/en/electrostatic-vs-conventional-painting-which-process-is-better/
[9] http://www.spiuserforum.com/index.php?threads%2Fconventional-spray-gun-vs-hvlp-turbine-paint-spray-system.1681%2F
[10] https://www.sprayequipment.com/blog/dispelling-the-2-primary-myths-about-electrostatic-sprayers
Hot Tags: China, Global, OEM, private label, manufacturers, factory, suppliers, manufacturing company