Content Menu
● Understanding Powder Supply Systems
>> Why the Right System Matters
● Key Considerations for Choosing a Powder Supply System
>> Material Characteristics
>> Production Requirements
>> Operational and Environmental Considerations
>> Regulatory and Safety Requirements
● Types of Powder Supply Systems
>> Pneumatic Conveying Systems
>> Mechanical Conveying Systems
>> Gravity-Based Systems
● Step-by-Step Selection Process
>> Step 1: Analyze Your Powder Properties
>> Step 2: Define Your Process Needs
>> Step 3: Evaluate System Options
>> Step 4: Assess Operational Factors
>> Step 5: Consider Future Expansion
>> Step 6: Engage with Experienced Suppliers
● Common Challenges and Solutions
>> Powder Flow Problems
>> Contamination and Product Loss
>> Static and Safety Hazards
● Industry-Specific Considerations
>> Pharmaceuticals
>> Food Processing
>> Chemical and Powder Coating
● Making the Final Decision
● Frequently Asked Questions (FAQs)
● Citations:
Selecting the right powder supply system is a crucial decision for businesses in industries such as pharmaceuticals, food processing, chemicals, and manufacturing. The efficiency, safety, and quality of your operations depend on a system that matches your specific material characteristics, production goals, and regulatory requirements. This comprehensive guide will walk you through the key considerations, system types, and decision-making criteria to help you choose the optimal powder supply system for your business.

Understanding Powder Supply Systems
Powder supply systems are engineered solutions designed to transport, store, and deliver powdered materials throughout a production process. These systems can range from simple gravity-fed hoppers to complex pneumatic conveying networks with integrated controls and dust management.
Why the Right System Matters
- Ensures consistent product quality
- Reduces operational downtime
- Minimizes material waste and contamination
- Enhances workplace safety and hygiene
- Supports scalability and future growth
Key Considerations for Choosing a Powder Supply System
To make an informed choice, you must assess several critical factors that influence system performance and suitability.
Material Characteristics
The properties of your powder directly impact the design and selection of the supply system. Consider the following:
- Particle Size and Distribution: Fine powders may cause dusting and clogging, while coarse particles require systems that prevent breakage and segregation.
- Bulk Density: Lightweight powders need different handling compared to denser materials, affecting conveying velocity and energy requirements.
- Flowability: Free-flowing powders are easier to handle, while cohesive or sticky powders may need agitation or aeration features.
- Abrasiveness and Sensitivity: Abrasive powders require wear-resistant components; heat- or moisture-sensitive powders may need inert gas blanketing or temperature control.
Production Requirements
- Conveying Distance and Rate: Longer distances and higher throughput demand more robust systems, such as pneumatic conveyors.
- Number of Inlets and Outlets: Multiple pick-up and discharge points influence system complexity and pipe design.
- Batch vs. Continuous Operation: Your process type affects the choice between batch feeders, continuous conveyors, or hybrid systems.
Operational and Environmental Considerations
- Hygiene and Cleanability: Industries like food and pharmaceuticals require systems with easy-to-clean, crevice-free designs and FDA-compliant materials.
- Dust Control: Enclosed systems minimize dust generation, protecting workers and maintaining product purity.
- Energy Efficiency: Evaluate the energy consumption of pneumatic versus mechanical systems for long-term cost savings.
- Scalability: Modular or flexible systems allow for future expansion as production demands grow.
Regulatory and Safety Requirements
- Explosion-Proof Design: For combustible powders, explosion-proof or ATEX-certified systems are essential.
- Grounding and Static Control: Proper grounding prevents static discharge and dust explosions, especially in powder coating and chemical processing.
Types of Powder Supply Systems
Understanding the main system types helps you match technology to your application.
Pneumatic Conveying Systems
- How They Work: Use air pressure or vacuum to transport powders through enclosed pipes.
- Advantages: Enclosed design reduces contamination and dust; suitable for long distances and high throughput; flexible routing.
- Variants:
- Dilute Phase: High-velocity air suspends and moves powders; ideal for non-abrasive, free-flowing materials.
- Dense Phase: Lower velocity, higher pressure; suitable for fragile or abrasive powders.
- Closed-Loop Systems: Use inert gas for hazardous or oxygen-sensitive materials.
Mechanical Conveying Systems
- Types: Screw conveyors, belt conveyors, bucket elevators.
- Advantages: Simple design, lower energy consumption, suitable for short distances and robust powders.
- Limitations: Higher risk of product degradation, less suitable for hazardous or dust-prone materials.
Gravity-Based Systems
- How They Work: Rely on gravity to move powders from higher to lower elevations.
- Advantages: No moving parts, minimal energy use, low maintenance.
- Limitations: Limited to specific plant layouts; not suitable for all materials.
Step-by-Step Selection Process
Step 1: Analyze Your Powder Properties
Conduct laboratory tests to determine particle size, bulk density, flowability, and sensitivity. This data will guide equipment selection and design features.
Step 2: Define Your Process Needs
Map out your production flow, including required throughput, number of transfer points, and integration with existing equipment.
Step 3: Evaluate System Options
Compare pneumatic, mechanical, and gravity-based systems based on your material and process requirements. Consider hybrid solutions if needed.
Step 4: Assess Operational Factors
- Space Constraints: Pneumatic systems are more compact, ideal for facilities with limited space.
- Cleanability: Select systems with easy access for cleaning and maintenance.
- Safety: Ensure compliance with industry safety standards and explosion prevention measures.
Step 5: Consider Future Expansion
Choose systems with modular designs or scalable capacity to accommodate business growth.
Step 6: Engage with Experienced Suppliers
Work with reputable manufacturers who can provide custom solutions, testing services, and after-sales support.
Common Challenges and Solutions
Powder Flow Problems
- Low Flow or Blockages: May result from poor feeder design or material buildup. Solutions include upgrading to larger feeders, adding vibration or aeration, or using anti-static coatings.
- Material Flooding: Excessive flow can be managed with slower feeders, vented hoppers, or discharge valves.
- Equipment Wear: Abrasive powders require reinforced systems and slower conveying speeds.
Contamination and Product Loss
- Solution: Use enclosed systems with dust collection and easy-clean features to minimize contamination and material loss.
Static and Safety Hazards
- Solution: Implement proper grounding, use anti-static materials, and install spark detection systems.
Industry-Specific Considerations
Pharmaceuticals
- Strict hygiene, dust containment, and validation requirements.
- Systems must be compatible with clean-in-place (CIP) protocols.
Food Processing
- FDA-compliant materials, easy cleaning, and allergen control are critical.
- Systems should prevent cross-contamination and maintain product integrity.
Chemical and Powder Coating
- Explosion-proof and anti-static features are essential.
- Systems must handle a wide range of powder properties and prevent segregation.
Making the Final Decision
Choosing the top powder supply system is a balance of technical, operational, and financial considerations. Prioritize:
- Material compatibility and product quality
- Process efficiency and reliability
- Safety and regulatory compliance
- Flexibility for future needs
Engage with suppliers who offer pilot testing, customization, and comprehensive support to ensure your investment delivers long-term value.
---
Frequently Asked Questions (FAQs)
1. What is the most important factor when choosing a powder supply system?
The most critical factor is the compatibility of the system with your powder's characteristics—such as particle size, flowability, and sensitivity. This ensures consistent, efficient, and safe operation.
2. How do I prevent dust and contamination in my powder supply system?
Opt for enclosed systems like pneumatic conveyors with integrated dust collection and easy-clean designs. Regular maintenance and proper sealing are also essential.
3. What are the benefits of pneumatic conveying over mechanical systems?
Pneumatic systems offer greater flexibility, better dust control, and are ideal for long-distance, high-throughput applications. They also reduce product contamination and operator exposure.
4. How can I ensure my system is future-proof?
Choose modular, scalable systems that can be expanded or reconfigured as your production needs grow. Engage with suppliers who offer upgrade paths and ongoing support.
5. What safety features should I look for in a powder supply system?
Look for explosion-proof components, proper grounding, anti-static materials, and dust containment features. For hazardous powders, consider systems with inert gas blanketing and spark detection.
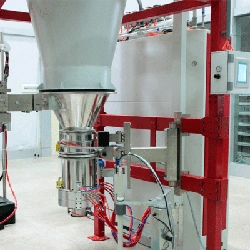
---
Citations:
[1] https://indpro.com/blog/powder-handling-systems-equipment-a-comprehensive-guide/
[2] https://pneumaticconveyors.net/powder-handling/
[3] https://macawberindia.in/powder-conveying-methods-benefits/
[4] https://www.powdercoating.org/page/FAQ
[5] https://www.apecusa.com/blog/troubleshooting-bulk-powder-flow-problems/
[6] https://www.ddpsinc.com/blog/choosing-the-right-powder-transfer-system-a-guide-to-key-performance-indicators
[7] https://ems-powdercoating.com/powder-coating-questions-and-answers/
[8] https://www.pneumaticconveyingsolutions.com/blog/powder-conveying-methods/
[9] https://www.customprocessingservices.com/blog/you-ask-we-answer-top-6-questions-about-food-powder-processing
[10] https://www.pfonline.com/articles/batch-system-vs-automated-line-powder-coating-systems
[11] https://reliantfinishingsystems.com/how-to-select-a-powder-coating-equipment-supplier/
[12] https://www.thermalspray.com/selecting-powder-coating-equipment-an-essential-guide/
[13] https://www.eaton.com/us/en-us/products/controls-drives-automation-sensors/industrial-control-center/atic/industrial-control---how-to/how-to-select-a-power-supply.html
[14] https://www.nordson.com/en/divisions/industrial-coating-systems/application-solutions/powder-coating
[15] https://www.precisiondipcoating.com/powder-coating-faq-answers-to-your-most-common-questions
[16] https://www.azpowder.com/blog/5-common-questions-about-powder-coating
[17] https://newfinishinc.com/10-frequently-asked-questions-about-powder-coatings-everything-you-need-to-know/
[18] https://www.slm-solutions.com/fileadmin/Content/Additive_Manufacturing/SLMSolutionsWhitePaper_7QuestionsToAskBeforeInvesting.pdf
[19] https://www.matconibc.com/faqs
---
来自 Perplexity 的回答: pplx.ai/share