Content Menu
● Introduction
● Understanding Powder Sieving: The Basics
>> What Is Powder Sieving?
>> Traditional Sieving Methods
>> Modern Powder Sieve Systems
● Comparing Efficiency: Modern vs. Traditional Sieving
>> Throughput and Processing Speed
>> Mesh Blinding and Downtime
>> Accuracy and Particle Size Control
>> Material Versatility
>> Ease of Use and Maintenance
● Cost-Effectiveness and Operational Impact
>> Labor and Operational Costs
>> Material Waste and Product Yield
>> Energy Consumption
>> Equipment Longevity and Maintenance
● Quality, Safety, and Regulatory Compliance
>> Product Quality and Consistency
>> Contaminant Removal and Safety
>> Hygienic Design
● Technological Advancements in Powder Sieving
>> Smart Technology Integration
>> Energy-Efficient Designs
>> Advanced Screen Materials
● Case Studies: Real-World Efficiency Gains
>> Food Processing
>> Pharmaceutical Manufacturing
>> Additive Manufacturing and Metal Powders
● Challenges and Considerations
>> Initial Investment
>> Training and Integration
>> Material-Specific Adjustments
● Conclusion: Is Our Powder Sieve System More Efficient?
● Frequently Asked Questions
● Citations:
Introduction
In the world of industrial manufacturing, the quality and consistency of powder materials are critical for product performance, safety, and regulatory compliance. Whether in pharmaceuticals, food processing, additive manufacturing, or powder coatings, the sieving process ensures that only particles of the desired size and purity make it into the final product. As industries evolve, so do the technologies supporting them. This article explores whether our modern powder sieve system outperforms traditional sieving methods, examining efficiency, accuracy, cost-effectiveness, and operational advantages.
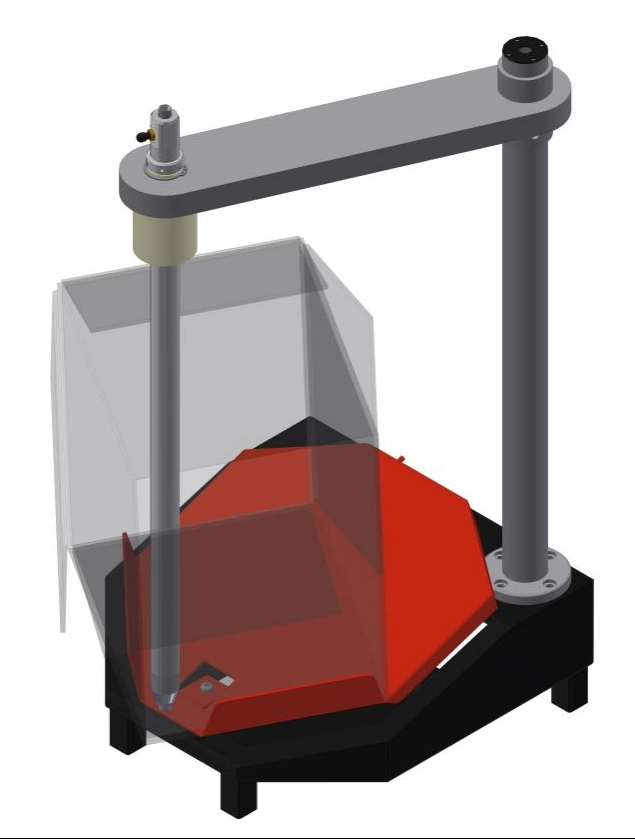
Understanding Powder Sieving: The Basics
What Is Powder Sieving?
Powder sieving is the process of separating particles based on size using a mesh or screen. The goal is to achieve uniform particle distribution, remove contaminants, and enhance the flow properties of powders. This process is essential across various industries, from pharmaceuticals and food to metal additive manufacturing and cosmetics.
Traditional Sieving Methods
Historically, powder sieving relied on manual or semi-automated techniques. These included:
- Handheld Sieves: Simple mesh screens shaken by hand, suitable for small batches.
- Stacked Sieve Shakers: Mechanical devices that oscillate a stack of sieves, each with different mesh sizes, to separate particles into fractions.
- Rotary Sifters: Machines using centrifugal force to propel powders against a screen, separating them by size.
While effective for their time, these methods often struggled with throughput, mesh blinding, inconsistent separations, and labor intensity.
Modern Powder Sieve Systems
Today's advanced powder sieve systems use high-frequency vibration, ultrasonic deblinding, and automated controls. Examples include:
- Vibratory Sieve Shakers: Employ high-frequency, multi-dimensional vibrations to rapidly separate particles.
- Ultrasonic Sieving Machines: Use ultrasonic waves to prevent mesh blinding and improve fine powder separation.
- High-Energy Sifters: Integrate powerful vibratory or centrifugal forces for ultra-fine and high-throughput applications.
These systems promise improved efficiency, accuracy, and ease of use.
Comparing Efficiency: Modern vs. Traditional Sieving
Throughput and Processing Speed
Modern powder sieve systems are engineered for high throughput. For instance, advanced vibratory or centrifugal sifters can process several times the volume of traditional machines without sacrificing accuracy. Some systems, like the Quadro FlexSift, have demonstrated up to seven times the capacity of conventional vibratory and horizontal sifters. This leap in efficiency allows manufacturers to meet higher production demands and reduce bottlenecks.
Traditional methods, especially manual or stacked sieve shakers, are inherently slower. They require more handling, frequent pauses for cleaning or mesh replacement, and are limited in the volume they can process per hour.
Mesh Blinding and Downtime
Mesh blinding—when particles clog the sieve mesh—is a significant cause of downtime in traditional sieving. Operators must stop production to clean or replace screens, leading to lost productivity and increased labor costs.
Modern systems address this with:
- High-Energy Vibration: Prevents particles from settling and clogging the mesh.
- Ultrasonic Deblinding: Uses ultrasonic waves to keep the mesh clear, even with ultra-fine powders.
- Automated Cleaning Cycles: Some systems feature self-cleaning mechanisms, further reducing manual intervention.
As a result, downtime is minimized, and the sieving process remains consistent and reliable.
Accuracy and Particle Size Control
Uniform particle size is vital for product quality, especially in applications like powder coatings, pharmaceuticals, and 3D printing. Traditional methods often struggle to maintain tight particle size distributions, particularly with fine or cohesive powders. Manual sieving is prone to human error and inconsistent results.
Modern powder sieve systems offer:
- Precise Mesh Control: Automated systems allow for quick changes and precise selection of mesh sizes.
- Consistent Separation: High-frequency vibrations and advanced screen materials ensure only particles of the desired size pass through.
- High Yield: Efficient separation reduces material loss and ensures that nearly 100% of the usable product is recovered.
Material Versatility
Traditional sieving methods can be limited by the type of powder processed. Sticky, electrostatic, or ultra-fine powders often cause problems such as agglomeration or static buildup, leading to poor separation and contamination.
Advanced sieve systems are designed to handle a wide range of materials, including:
- Metal powders for additive manufacturing
- Pharmaceutical ingredients
- Food powders (e.g., flour, spices)
- Plastics and ceramics
Their adaptability makes them indispensable for modern, multi-product manufacturing environments.
Ease of Use and Maintenance
Traditional sieves require frequent manual cleaning, mesh replacement, and calibration. This increases labor costs and the risk of operator error.
Modern systems are designed for:
- Quick Screen Changes: Tool-free or bolt-locking mechanisms allow for rapid mesh replacement.
- Easy Cleaning: Fewer parts and smooth surfaces simplify cleaning and reduce cross-contamination risks.
- Automated Operation: One-button operation and programmable cycles reduce the need for skilled labor and training.
Cost-Effectiveness and Operational Impact
Labor and Operational Costs
Automated powder sieve systems dramatically reduce labor requirements. Operators can oversee multiple machines simultaneously, and the need for manual intervention is minimized. This not only lowers direct labor costs but also reduces the risk of human error and workplace injuries.
Material Waste and Product Yield
Efficient sieving means less material is wasted. Modern systems ensure that only the desired fractions are separated, and nearly all usable material is recovered. In contrast, traditional methods often result in higher losses due to mesh blinding, incomplete separation, or contamination.
Energy Consumption
While advanced sieve systems may require more initial power due to high-frequency vibration or ultrasonic components, their faster processing times and reduced downtime often translate into lower overall energy consumption per unit of material processed.
Equipment Longevity and Maintenance
High-quality modern sieve systems are built for durability, with robust materials and fewer moving parts prone to wear. Features like stainless steel construction and dust-tight connections extend equipment life and reduce the frequency and cost of repairs.
Quality, Safety, and Regulatory Compliance
Product Quality and Consistency
Modern powder sieve systems deliver superior product consistency, which is essential for:
- Pharmaceutical dosage accuracy
- Food texture and safety
- Uniform coatings in manufacturing
- Reliable 3D printing results
Contaminant Removal and Safety
Automated sieving systems are highly effective at removing foreign particles, lumps, and contaminants. This is crucial for meeting regulatory standards in food, pharmaceuticals, and other sensitive industries.
Hygienic Design
Modern systems are designed with hygiene in mind:
- Smooth, non-porous surfaces for easy cleaning
- Minimal crevices to prevent bacterial growth
- Compliance with industry standards (e.g., FDA, ATEX, cGMP)
These features ensure that each batch meets stringent health and safety requirements.
Technological Advancements in Powder Sieving
Smart Technology Integration
Some advanced sieve systems feature:
- Real-time monitoring and remote control
- Predictive maintenance alerts
- Data logging for quality assurance
These innovations help operators optimize performance and anticipate maintenance needs, further improving efficiency and reducing unplanned downtime.
Energy-Efficient Designs
Modern sieve systems are increasingly designed for energy efficiency, reducing operational costs and supporting sustainability initiatives.
Advanced Screen Materials
New materials, such as high-grade stainless steel and specialized polymers, offer improved durability, chemical resistance, and performance, ensuring consistent operation and a longer equipment lifespan.
Case Studies: Real-World Efficiency Gains
Food Processing
In food powder processing, industrial vibrating sifters have become essential for ensuring product consistency, removing impurities, and meeting regulatory standards. These machines have enabled manufacturers to scale up production without sacrificing quality, reduce labor costs, and minimize waste.
Pharmaceutical Manufacturing
Pharmaceutical companies rely on advanced sieving systems for precise particle size control and contaminant removal. The result is improved product safety, dosage accuracy, and compliance with regulatory requirements.
Additive Manufacturing and Metal Powders
The additive manufacturing industry demands ultra-fine, consistent metal powders. Modern high-energy sieve systems have enabled manufacturers to achieve tight particle size distributions, reduce material waste, and improve the quality of printed parts.
Challenges and Considerations
Initial Investment
Modern powder sieve systems can require a significant upfront investment compared to traditional methods. However, the long-term savings in labor, maintenance, and material waste often justify the cost.
Training and Integration
Operators may require training to use advanced systems effectively. Integration into existing production lines should be carefully planned to maximize benefits.
Material-Specific Adjustments
While modern systems are highly versatile, some materials may require specific mesh sizes, vibration frequencies, or cleaning protocols to achieve optimal results.
Conclusion: Is Our Powder Sieve System More Efficient?
The evidence is clear: modern powder sieve systems offer substantial efficiency gains over traditional methods. They deliver higher throughput, reduced downtime, superior accuracy, and lower operational costs. Their ability to handle a wide range of materials, combined with ease of use, hygienic design, and smart technology integration, makes them indispensable for today's demanding manufacturing environments.
While the initial investment may be higher, the long-term benefits—improved product quality, regulatory compliance, and profitability—make advanced powder sieving systems the superior choice for most industrial applications.
---
Frequently Asked Questions
1. What are the main advantages of a modern powder sieve system over traditional methods?
Modern powder sieve systems offer higher throughput, reduced downtime due to mesh blinding prevention, superior particle size control, and automation that minimizes labor and maintenance requirements.
2. How does mesh blinding affect sieving efficiency, and how do modern systems address this issue?
Mesh blinding occurs when particles clog the sieve mesh, reducing throughput and requiring manual cleaning. Modern systems use high-frequency vibration or ultrasonic waves to prevent blinding, ensuring consistent performance and minimal downtime.
3. Are modern powder sieve systems suitable for all types of powders?
Yes, advanced systems are designed to handle a wide variety of powders, including fine, sticky, or electrostatic materials, making them suitable for industries like food, pharmaceuticals, metals, and plastics.
4. What is the impact of automated sieving on product quality and safety?
Automated sieving ensures uniform particle size, removes contaminants, and reduces human error, leading to higher product quality and improved safety, particularly in regulated industries.
5. Is the higher initial investment in a modern sieve system justified?
While the upfront cost is greater, the long-term savings in labor, reduced waste, improved yield, and lower maintenance costs typically result in a strong return on investment.

---
Citations:
[1] https://elcanindustries.com/blog_posts/powder-coating-sieves-what-are-the-pros-and-cons-heres-what-you-need-to-know/
[2] https://blog.praterindustries.com/sieving-techniques-industrial-sieves-vs.-rotary-sifters
[3] https://elcanindustries.com/blog_posts/ultrasonic-sieving-machines-heres-what-you-should-know/
[4] https://production-to-go.com/en/manufacturers/sinterit/powder-sieve/overview
[5] https://blog.wstyler.com/particle-analysis/considerations-when-choosing-a-sieve-shaker
[6] https://www.gemapowdercoating.com/en/support/tips-tricks/sieve-problems
[7] https://www.tcipowder.com/resources/troubleshooting-guide/chapter-thirteen-tci-troubleshooting-guide/
[8] https://www.sciencedirect.com/science/article/abs/pii/S0032591009002228
[9] https://vibrascreener.com/top-benefits-of-industrial-vibrating-sifters-in-food-powder-processing/
[10] https://www.russellfinex.com/en/news-and-events/sieving-powders/
[11] https://www.quadro-mpt.com/news-and-events/the-flexsift
[12] https://www.pharmaguideline.com/2007/02/official-standards-of-powders-sieves-size-separation.html
[13] https://www.innovabiomed.com/2930.html
[14] https://www.allpackchina.com/powder-sieving-machine/
[15] https://ems-powdercoating.com/powder-coating-questions-and-answers/
[16] https://elcanindustries.com/metal-powder-sieve/
[17] https://international-pharma.com/wp-content/uploads/2012/12/4-Uses-of-Sieves-in-the-Pharmaceutical-Industry-and-the-Increased-Demand-for-Containment.pdf
[18] https://bulkinside.com/bulk-solids-handling/screening-separation/metal-powder-sieving-station-for-additive-manufacturing/
[19] https://www.nordson.com/en/products/industrial-coating-systems-products/nrps-200---rotary-powder-coating-sieve
[20] https://pharma-industry-review.com/pharmaceutical-grinding-and-sieving-technology-trends-in-2021
[21] https://www.airpower-usa.com/wp-content/uploads/2019/08/Powder-Coating-Troubleshoothing-revised-7-10-14.pdf
[22] https://www.globalgilson.com/blog/factoring-flowability-sieving-sizing
[23] https://www.palamaticprocess.com/blog/sieving
[24] https://www.news-medical.net/whitepaper/20240731/Current-trends-in-grinding-and-sieving-technology.aspx
[25] https://www.munit.com/other-services/sieving.html5
[26] https://www.mt.com/gb/en/home/applications/Laboratory_weighing/sieve-analysis.html
[27] https://www.molecular-sieve.cc/faq/
---
Hot Tags: China, Global, OEM, private label, manufacturers, factory, suppliers, manufacturing company