Content Menu
● Understanding Powder Supply Systems
● Key Factors to Consider When Choosing a Powder Supply System
>> Product Characteristics
>>> Bulk Density and Weight
>>> Particle Size Distribution
>>> Flowability and Angle of Repose
>> Material Compatibility and Sensitivity
>> Conveying Dynamics and System Performance
>>> Conveying Velocity and Pressure
>>> Operating Modes
>> Environmental and Operational Considerations
>>> Dust Control and Safety
>>> Energy Efficiency
>>> Scalability and Flexibility
● Types of Powder Supply Systems
>> Pneumatic Conveying Systems
>> Mechanical Conveying Systems
>> Gravity-Based Systems
>> Dosing and Feeding Equipment
● Steps to Determine the Best Powder Supply System
>> 1. Define Your Application Requirements
>> 2. Evaluate Powder Characteristics
>> 3. Assess System Options Against Key Performance Indicators (KPIs)
>> 4. Consult with Experts and Integrators
>> 5. Plan for Testing and Validation
● Common Challenges and How to Overcome Them
● Frequently Asked Questions
In many industries, from pharmaceuticals and food processing to micropropulsion and manufacturing, selecting the right powder supply system is crucial for operational efficiency, safety, and product quality. With a wide variety of powder handling and transfer technologies available, making the best choice requires a thorough understanding of your specific needs and the characteristics of the powders you work with. This article will guide you through the key factors and considerations to help you determine the best powder supply system for your application.
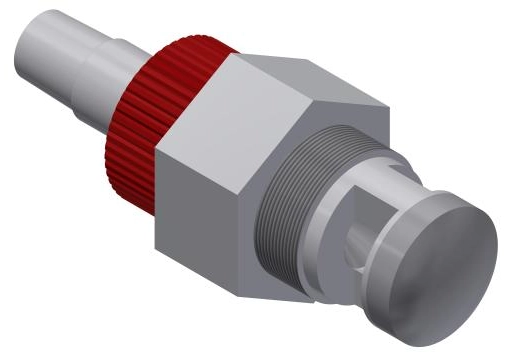
Understanding Powder Supply Systems
Powder supply systems are designed to transfer, feed, or dose powders safely and efficiently from one point to another within a production process. These systems can vary widely, including pneumatic conveying, mechanical feeders, gravity-based systems, and specialized dosing equipment. Each system type has its advantages and limitations depending on the powder's physical properties and the operational requirements.
Key Factors to Consider When Choosing a Powder Supply System
Product Characteristics
Bulk Density and Weight
The bulk density of your powder significantly influences the choice of supply system. Lightweight powders require gentle handling to avoid over-aeration or segregation, while denser powders may need more robust conveying mechanisms with higher energy input to maintain flow. Ensuring the system can handle your powder's weight without compromising integrity is essential.
Particle Size Distribution
Powders with fine particles may generate dust, cause clogging, or require dust control measures, whereas coarse powders might be prone to breakage during transfer. Understanding the size distribution helps in selecting equipment that minimizes product degradation and maintains consistent flow.
Flowability and Angle of Repose
The flow behavior of powders ranges from free-flowing to cohesive or sticky. Powders with poor flowability may need systems equipped with agitation, vibration, or aeration features to prevent bridging and ensure steady transfer. The angle of repose, which indicates how a powder naturally settles, affects hopper design and feeding mechanisms.
Material Compatibility and Sensitivity
Some powders are heat-sensitive, hygroscopic (absorbing moisture), or prone to oxidation. Such powders require specialized handling systems with features like temperature control, inert gas blanketing, or moisture barriers to maintain quality during transfer. Additionally, abrasive powders necessitate wear-resistant materials for system components to reduce maintenance costs.
Conveying Dynamics and System Performance
Conveying Velocity and Pressure
The velocity at which powder is conveyed must be optimized; too high can cause product degradation and equipment wear, too low can lead to blockages. Understanding the pressure drop across the conveying line helps in designing a system that operates efficiently without excessive energy consumption.
Operating Modes
Some advanced systems offer continuous or pulsed operation modes. For example, in micropropulsion applications, pulsed operation can achieve significantly higher powder flow rates and better powder-to-carrier gas mass flow ratios, improving performance.
Environmental and Operational Considerations
Dust Control and Safety
In industries with strict hygiene or safety standards, dust containment is critical. Systems with integrated dust collection or sealed designs help minimize contamination risks and maintain safe work environments.
Energy Efficiency
Energy consumption is a growing concern. Pneumatic systems often require more energy than mechanical alternatives. Selecting an energy-efficient system can reduce operational costs and environmental impact.
Scalability and Flexibility
If your production volume is expected to grow, choosing a modular or flexible system that can scale with your needs is a wise investment. This avoids costly upgrades or replacements in the future.
Types of Powder Supply Systems
Pneumatic Conveying Systems
These systems use air pressure or vacuum to move powders through pipelines. They are suitable for long distances and can be designed for closed, dust-free transfer. However, they may consume more energy and can cause powder degradation if not properly configured.
Mechanical Conveying Systems
Mechanical conveyors such as screw feeders, belt conveyors, or vibratory feeders physically move powder. They tend to be more energy-efficient and gentler on powders but are generally limited to shorter distances and require more space.
Gravity-Based Systems
These systems rely on gravity to move powders, often used for simple transfer tasks with free-flowing powders. They are low-cost and low-maintenance but are limited in application scope.
Dosing and Feeding Equipment
For precise powder supply, dosing equipment such as volumetric or gravimetric feeders ensure accurate and consistent powder delivery. Choosing the right dosing equipment depends on required accuracy, powder characteristics, and production speed.
Steps to Determine the Best Powder Supply System
1. Define Your Application Requirements
Start by clearly outlining your production goals, powder characteristics, throughput requirements, and environmental constraints. Consider factors such as:
- Powder type and properties (density, particle size, flowability)
- Required transfer distance and elevation changes
- Accuracy and consistency needs
- Safety and hygiene standards
- Energy consumption targets
- Budget and scalability plans
2. Evaluate Powder Characteristics
Conduct thorough testing of your powder's bulk density, particle size distribution, flowability, angle of repose, and sensitivity to environmental factors. This data will guide the selection of system components and configurations.
3. Assess System Options Against Key Performance Indicators (KPIs)
Compare potential systems based on KPIs such as:
- Transfer efficiency and throughput capacity
- Product integrity and degradation risk
- Energy consumption
- Maintenance requirements and durability
- Dust control effectiveness
- Ease of operation and integration with existing processes
4. Consult with Experts and Integrators
Partnering with experienced system integrators can help tailor solutions to your specific needs. Integrators provide valuable insights into potential challenges and can design systems that optimize performance while controlling costs.
5. Plan for Testing and Validation
Before full-scale implementation, conduct pilot tests or trials to validate system performance with your powder under real operating conditions. Adjust system parameters as needed to achieve optimal results.
Common Challenges and How to Overcome Them
- Powder Segregation: Use gentle conveying methods and optimize velocity to prevent separation of particle sizes.
- Dust Generation: Implement sealed transfer systems and dust collection to maintain safety and cleanliness.
- Equipment Wear: Select wear-resistant materials and coatings when handling abrasive powders.
- Flow Blockages: Incorporate vibration or agitation features to maintain consistent powder flow.
- Cost Overruns: Balance initial investment with long-term operational savings by focusing on system efficiency and reliability rather than just upfront cost.
Frequently Asked Questions
Q1: How do I know if pneumatic or mechanical conveying is better for my powder?
A1: Pneumatic conveying is ideal for long distances and dust-sensitive environments but uses more energy. Mechanical conveying is more energy-efficient and gentler but suited for shorter distances. Consider powder properties and process layout when choosing.
Q2: What role does powder flowability play in system selection?
A2: Flowability affects how easily powder moves through equipment. Poor flowability requires systems with agitation or aeration to prevent blockages and ensure consistent supply.
Q3: How important is dust control in powder supply systems?
A3: Dust control is critical for safety, hygiene, and product quality, especially in pharmaceuticals and food industries. Systems with sealed transfer and dust collection reduce contamination risks.
Q4: Can powder supply systems be customized for specific powders?
A4: Yes, systems can be tailored based on powder characteristics such as sensitivity, abrasiveness, and particle size to optimize performance and durability.
Q5: What should I consider regarding scalability when choosing a powder supply system?
A5: Choose modular or flexible systems that can adapt to increased production volumes or process changes to avoid costly future upgrades.

[1] https://forum.accurateshooter.com/threads/powder-selection-how-do-you-choose.4024160/
[2] https://www.longrangehunting.com/threads/best-way-to-find-powder-charge.319518/
[3] https://brodie-gitea.revolution.ca/the-ultimate-guide-to-finding-the-best-auto-powder-reloading-systems/
[4] https://www.youtube.com/watch?v=cB5F8oneRB8
[5] https://www.ddpsinc.com/blog/choosing-the-right-powder-transfer-system-a-guide-to-key-performance-indicators
[6] https://www.jstage.jst.go.jp/article/kona/advpub/0/advpub_2026005/_article/-char/en
[7] https://www.magnumsystems.com/2022/01/powder-transfer-system/
[8] https://www.processingmagazine.com/material-handling-dry-wet/weighers-feeders/article/53069548/five-questions-to-ask-when-selecting-powder-dosing-equipment
[9] https://www.metalformingmagazine.com/article/?%2Fmetal-powders%2Fother%2Fsix-points-to-consider-for-better-powder
Hot Tags: China, Global, OEM, private label, manufacturers, factory, suppliers, manufacturing company