Content Menu
● What Is Powder Coating?
● The Basic Principles of Powder Coating
>> Electrostatic Spray Deposition (ESD)
>> Melt Curing
● Step-by-Step Powder Coating Process
>> 1. Surface Preparation
>> 2. Powder Application
>> 3. Curing
>> 4. Cooling and Inspection
● Controlling Film Thickness and Quality
● Advantages of Powder Coating Systems
● Applications of Powder Coating
● Common Types of Powder Coatings
● Summary
● Related Questions and Answers
● Citations:
Powder coating is a widely used finishing process that offers durable, high-quality coatings for various metal and non-metal surfaces. Unlike traditional liquid paints, powder coating uses a dry powder that is applied electrostatically and then cured under heat to form a solid, protective layer. This article will explore the detailed workings of a powder coating system, including its principles, application methods, curing process, and quality control measures.
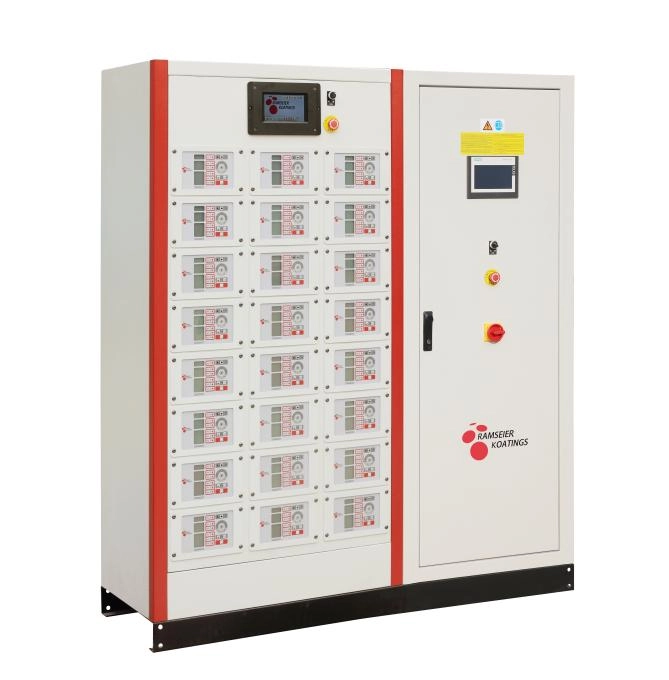
What Is Powder Coating?
Powder coating is a dry finishing technique where fine powder particles are applied to a surface to create a protective and decorative finish. The powder typically consists of polymer resins, pigments, and additives that provide color and durability. The key advantage of powder coating over liquid paint is that it produces a thicker, more uniform coating in a single application without the need for solvents, making it environmentally friendly and efficient.
The Basic Principles of Powder Coating
Electrostatic Spray Deposition (ESD)
The core principle behind powder coating is electrostatic attraction. The powder particles are given an electrostatic charge as they pass through a specialized spray gun. The object to be coated, usually metal, is grounded, creating an opposite charge. This difference in charge causes the powder particles to be attracted to and adhere uniformly on the surface of the object.
The electrostatic charge ensures that the powder wraps around the object, even on complex shapes, providing an even coating. This process is called Electrostatic Spray Deposition (ESD) and is the most commonly used method for applying powder coatings.
Melt Curing
Once the powder particles have adhered to the surface, the coated part is heated in an oven. The heat causes the powder to melt, flow, and chemically react (cure), forming a continuous, durable film. This curing process solidifies the coating, giving it excellent resistance to corrosion, chemicals, and wear.
Step-by-Step Powder Coating Process
1. Surface Preparation
Proper surface preparation is crucial for powder coating to ensure good adhesion and a flawless finish. The process typically involves:
- Cleaning: Removing oils, dirt, and contaminants using chemical cleaners (acidic, alkaline, or neutral solutions).
- Mechanical Treatment: Techniques like sandblasting or shot blasting create a rough surface profile (anchor pattern) to improve powder adhesion.
- Rinsing and Drying: The parts are rinsed to remove residues and dried in ovens at low temperatures to prepare for coating.
2. Powder Application
The powder application is performed using one of several methods:
- Electrostatic Spray Deposition (ESD): The most common method involves spraying charged powder particles onto a grounded part using an electrostatic spray gun.
- Fluidized Bed Coating: The part is preheated and dipped into a bed of fluidized powder particles. The heat melts the powder, coating the part evenly.
- Electrostatic Fluidized Bed Coating: Combines electrostatic charging with fluidized bed dipping for enhanced coating control.
In ESD, the powder particles are charged negatively as they exit the spray gun, while the part is grounded positively. This charge difference causes the powder to be attracted and stick to the surface.
3. Curing
After powder application, the coated parts are placed in a curing oven, typically heated between 160°C and 200°C (320°F to 390°F). The curing time varies but usually lasts around 10 to 20 minutes depending on the powder type and part size.
During curing:
- The powder melts and flows to form a smooth, continuous film.
- Chemical cross-linking reactions occur, solidifying the coating.
- The coating cools to form a hard, durable surface.
4. Cooling and Inspection
Once cured, parts are cooled to room temperature. The coating is inspected for uniformity, thickness, color, and defects. Thickness control is essential to ensure the coating meets performance requirements.
Controlling Film Thickness and Quality
Film thickness control is vital to the performance and appearance of the powder coating. Several factors influence thickness:
- Spray Distance: Closer spray gun distance results in thicker coatings.
- Spray Speed: Slower spray speeds deposit more powder, increasing thickness.
- Powder Particle Size and Flow Rate: Smaller particles and higher flow rates produce thicker coatings.
- Multi-layer Coating: Applying multiple layers can achieve desired thickness precisely.
- Thickness Measurement: Instruments measure coating thickness in real-time, allowing adjustments during application.
Proper control ensures the coating is neither too thin (leading to poor protection) nor too thick (causing defects like cracking or peeling).
Advantages of Powder Coating Systems
- Environmental Benefits: No solvents or volatile organic compounds (VOCs) are released, making it eco-friendly.
- Durability: Powder coatings provide excellent resistance to chipping, scratching, fading, and corrosion.
- Efficiency: High transfer efficiency with up to 90% powder utilization when reclaim systems are used.
- Variety: Available in many colors, textures, and special effects.
- Cost-Effective: Lower overall energy consumption and faster processing compared to liquid painting.
Applications of Powder Coating
Powder coating is widely used in industries such as automotive, appliances, architecture, furniture, and metal fabrication. It is ideal for coating metal parts like automotive wheels, outdoor furniture, metal cabinets, and machinery components.
Common Types of Powder Coatings
- Thermoset Powders: These powders cure chemically during baking and cannot be remelted. Examples include epoxy, polyester, and hybrid powders.
- Thermoplastic Powders: These powders melt and flow upon heating but do not chemically cure. They can be reheated and reshaped.
Summary
A powder coating system works by applying dry powder particles electrostatically to a grounded surface, followed by curing the powder through heat to form a durable, protective coating. The process involves careful surface preparation, powder application via electrostatic spray or fluidized bed, curing in an oven, and quality control to ensure proper film thickness and finish. This technology offers environmental advantages, superior durability, and cost-effectiveness, making it a preferred choice for many industrial coating applications.
Related Questions and Answers
Q1: What materials can be powder coated?
A1: Most metals are ideal for powder coating due to their conductivity and heat resistance. Some thermoplastics and composites can also be powder coated using specialized processes.
Q2: How long does the powder coating process take?
A2: The entire process, including preparation, application, and curing, typically takes from a few minutes to an hour depending on part size and complexity.
Q3: Can powder coating be applied in multiple colors?
A3: Yes, powder coating can be applied in multiple layers or masked for multi-color finishes, though this requires careful process control.
Q4: Is powder coating environmentally friendly?
A4: Yes, powder coating releases no solvents or VOCs and allows for high powder utilization, making it more environmentally friendly than traditional painting.
Q5: How durable is a powder coating compared to liquid paint?
A5: Powder coatings generally offer superior durability, including better resistance to chipping, scratching, and corrosion compared to liquid paints.

Citations:
[1] https://metaltech.us/blog/powder-coating-101-how-does-it-work/
[2] https://www.keystonekoating.com/blog/guide-to-powder-coating/
[3] https://www.youtube.com/watch?v=l3VF6C1_RGg
[4] https://www.tiger-coatings.com/us-en/blog/powder-coating-process
[5] https://www.powderspraymachine.com/powder-coating-principle-and-film-thickness-control-method/
[6] https://patents.google.com/patent/CN115707332A/en
[7] https://hydram.co.uk/technical/powder-coating-technology/
[8] https://patents.google.com/patent/CN1289273A/zh
Hot Tags: China, Global, OEM, private label, manufacturers, factory, suppliers, manufacturing company