Content Menu
● The Growing Complexity of Modern Coating Lines
>> Challenges Faced Without Smart Data Management
● What Is a Smart Data Management System?
>> Core Features
● Why Smart Data Management Is Essential for Coating Lines
>> 1. Enhancing Process Control and Quality Assurance
>> 2. Reducing Downtime and Maintenance Costs
>> 3. Improving Compliance and Traceability
>> 4. Increasing Operational Efficiency
>> 5. Supporting Sustainable and Smart Coating Technologies
● Key Benefits of Integrating a Smart Data Management System in Coating Lines
● How Smart Data Management Transforms Coating Line Operations
>> H2: Real-Time Data Analysis for Proactive Management
>> H3: Early Detection of Anomalies
>> H3: Increased Agility and Flexibility
>> H2: Eliminating Data Silos to Improve Visibility and Decision-Making
>> H3: Unified Data Systems
>> H3: Simplified Communication and Collaboration
>> H2: Traceability and Compliance Management
>> H3: Automated Documentation
>> H3: Audit and Review Simplification
>> H2: Predictive Maintenance and Cost Savings
>> H3: Extending Equipment Life
>> H3: Minimizing Unplanned Downtime
>> H2: Supporting Advanced Coating Technologies
>> H3: Ensuring Optimal Application Conditions
>> H3: Long-Term Performance Tracking
● Conclusion
● Frequently Asked Questions
In today's highly competitive manufacturing environment, coating lines play a crucial role in ensuring product quality, durability, and aesthetic appeal. However, managing the vast amount of data generated during coating processes can be challenging. This is where a smart data management system becomes indispensable. It not only streamlines operations but also enhances decision-making, reduces costs, and improves product consistency.
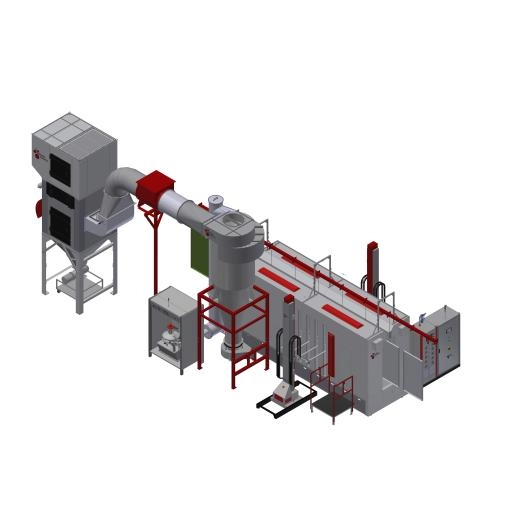
The Growing Complexity of Modern Coating Lines
Modern coating lines involve multiple steps such as surface preparation, application, curing, and inspection. Each stage generates critical data points including temperature, humidity, coating thickness, curing time, and inspection results. Managing this data manually or with fragmented systems leads to inefficiencies and errors.
Challenges Faced Without Smart Data Management
- Data Silos: Different departments or machines often store data separately, making it difficult to get a holistic view of the process.
- Inconsistent Data Quality: Manual data entry or incompatible systems can lead to errors and unreliable information.
- Delayed Decision-Making: Lack of real-time data visibility slows down responses to process deviations or equipment issues.
- Compliance Risks: Inadequate data tracking can compromise quality assurance and regulatory compliance.
What Is a Smart Data Management System?
A smart data management system integrates data collection, storage, analysis, and reporting into a unified platform tailored for coating lines. It uses automation, connectivity, and analytics to provide real-time insights and traceability throughout the coating process.
Core Features
- Real-Time Process Visibility: Continuous monitoring of key parameters enables immediate detection of anomalies.
- Data Integration: Combines data from sensors, machines, inspection tools, and enterprise systems.
- Traceability and Documentation: Automatically records process conditions and inspection results for quality audits.
- Predictive Analytics: Uses historical data to predict maintenance needs and optimize process parameters.
- User-Friendly Interfaces: Dashboards and alerts help operators and managers make informed decisions quickly.
Why Smart Data Management Is Essential for Coating Lines
1. Enhancing Process Control and Quality Assurance
Coating quality depends on precise control of multiple variables. Smart data management systems provide continuous monitoring and feedback, allowing operators to adjust parameters instantly to maintain optimal conditions. This reduces defects such as uneven coating thickness, poor adhesion, or curing failures.
2. Reducing Downtime and Maintenance Costs
By analyzing data trends, smart systems can predict equipment wear or failures before they cause unplanned downtime. Predictive maintenance scheduling based on real-time data helps avoid costly breakdowns and extends the life of coating line machinery.
3. Improving Compliance and Traceability
Coating processes often require adherence to strict industry standards and customer specifications. Smart data management ensures every batch is fully documented with process parameters and inspection results, simplifying audits and certification processes.
4. Increasing Operational Efficiency
Eliminating data silos and automating data collection reduces manual paperwork and errors. Operators spend less time on administrative tasks and more on optimizing production. Unified data access facilitates better coordination across departments such as production, quality, and maintenance.
5. Supporting Sustainable and Smart Coating Technologies
Advanced coatings, such as smart or environmentally friendly coatings, require precise application and monitoring to deliver their benefits, including corrosion protection and reduced environmental impact. Smart data management systems enable on-demand adjustments and long-term performance tracking of these coatings.
Key Benefits of Integrating a Smart Data Management System in Coating Lines
Benefit | Description |
Real-Time Visibility | Live monitoring of process variables to quickly identify and correct deviations. |
Data Accuracy and Integrity | Automated data capture reduces errors and ensures reliable records. |
Predictive Maintenance | Early detection of equipment issues to prevent downtime and reduce repair costs. |
Improved Collaboration | Shared data access breaks down silos, enhancing communication between teams. |
Regulatory Compliance | Comprehensive traceability supports quality assurance and audit readiness. |
Cost Reduction | Optimized processes and reduced waste lower operational expenses. |
Enhanced Product Quality | Consistent process control leads to superior coating performance and customer satisfaction. |
How Smart Data Management Transforms Coating Line Operations
H2: Real-Time Data Analysis for Proactive Management
Real-time data analysis allows manufacturers to detect anomalies early and take corrective actions before defects occur or equipment fails. This proactive approach minimizes scrap rates and avoids costly rework.
H3: Early Detection of Anomalies
Sensors continuously monitor parameters such as temperature, humidity, and coating thickness. When values deviate from set thresholds, alerts notify operators to intervene immediately.
H3: Increased Agility and Flexibility
With instant access to process data, production teams can quickly adapt to changes in raw materials, environmental conditions, or customer requirements, maintaining consistent quality.
H2: Eliminating Data Silos to Improve Visibility and Decision-Making
Data silos occur when information is trapped in isolated systems or departments, hindering collaboration and slowing decisions.
H3: Unified Data Systems
Smart data management platforms unify data from various sources, providing a single source of truth. This transparency enables faster, more accurate decisions and better coordination across production, quality, and supply chain teams.
H3: Simplified Communication and Collaboration
When all stakeholders have access to the same up-to-date information, communication improves, reducing misunderstandings and delays.
H2: Traceability and Compliance Management
Traceability is critical for quality assurance and regulatory compliance in coating applications.
H3: Automated Documentation
Smart systems automatically log all relevant process data and inspection results, creating a comprehensive record for each production batch.
H3: Audit and Review Simplification
Having organized, accessible data simplifies internal audits and external inspections, reducing the risk of non-compliance penalties.
H2: Predictive Maintenance and Cost Savings
Predictive maintenance leverages data analytics to forecast equipment failures and schedule maintenance proactively.
H3: Extending Equipment Life
By addressing issues early, manufacturers avoid major repairs and extend the operational lifespan of coating line machinery.
H3: Minimizing Unplanned Downtime
Scheduled maintenance based on real-time data reduces unexpected breakdowns, keeping production on schedule and lowering costs.
H2: Supporting Advanced Coating Technologies
Smart coatings, which can detect corrosion or deliver inhibitors on demand, require precise application and monitoring.
H3: Ensuring Optimal Application Conditions
Smart data management systems monitor environmental and process parameters to ensure these advanced coatings perform as intended.
H3: Long-Term Performance Tracking
Data collected over time helps evaluate coating effectiveness and schedule maintenance or recoating before failures occur.
Conclusion
A smart data management system is no longer a luxury but a necessity for modern coating lines. It enhances process control, improves product quality, reduces downtime, ensures compliance, and supports the integration of advanced coating technologies. By breaking down data silos and providing real-time insights, these systems empower manufacturers to optimize operations, reduce costs, and stay competitive in a rapidly evolving market.
Frequently Asked Questions
Q1: What types of data are managed in a smart data management system for coating lines?
A1: It manages process parameters (temperature, humidity, coating thickness), equipment status, inspection results, and environmental conditions.
Q2: How does smart data management improve coating quality?
A2: By providing real-time monitoring and feedback, it enables immediate adjustments to maintain optimal coating conditions, reducing defects.
Q3: Can smart data management systems help with regulatory compliance?
A3: Yes, they automatically document all process and inspection data, simplifying audits and ensuring traceability.
Q4: What is predictive maintenance, and how does it benefit coating lines?
A4: Predictive maintenance uses data analytics to forecast equipment failures, allowing proactive repairs that reduce downtime and costs.
Q5: Are smart data management systems compatible with advanced coatings like smart or environmentally friendly coatings?
A5: Absolutely, these systems ensure precise application conditions and monitor long-term coating performance to maximize benefits.
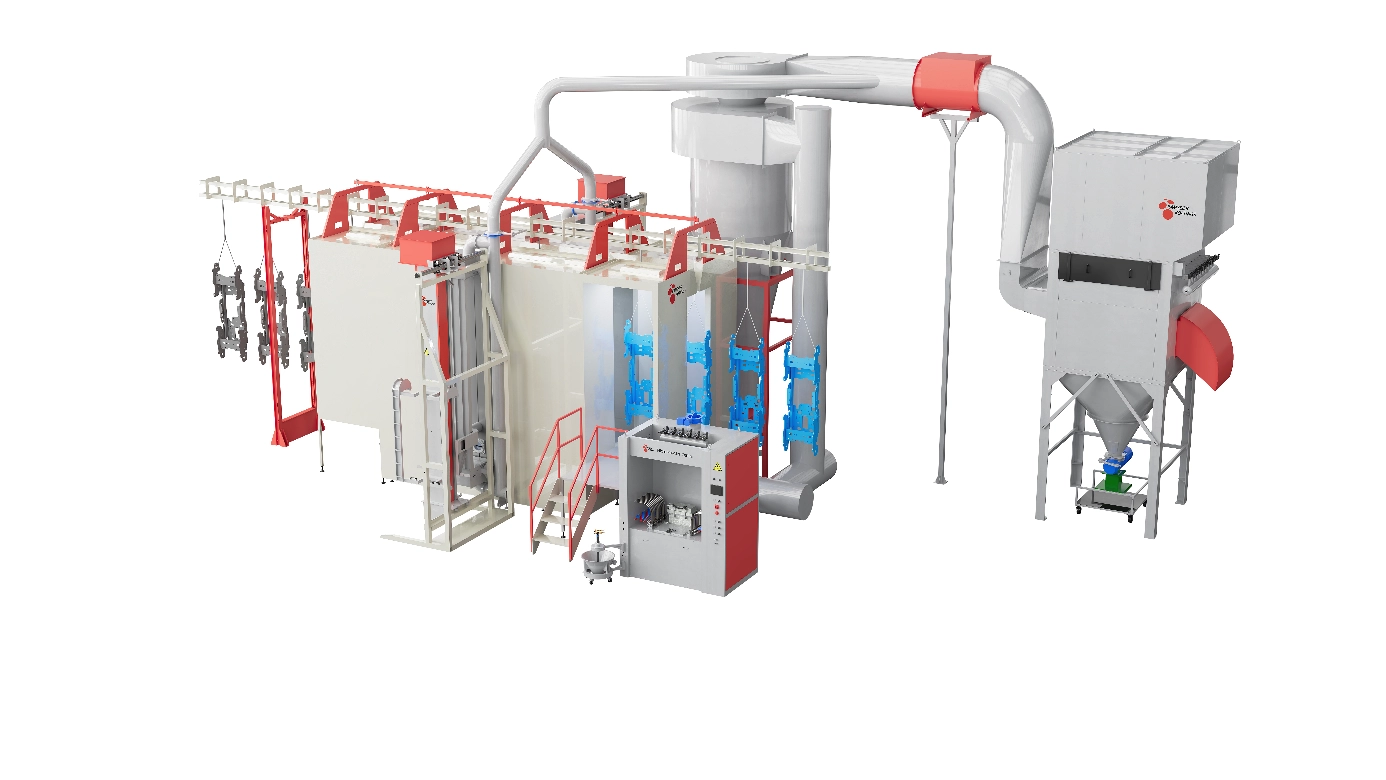
[1] https://www.paint.org/coatingstech-magazine/articles/smart-coatings-reaching-big-time-many-opportunities/
[2] https://patents.google.com/patent/CN106021209A/zh
[3] https://www.ramseierkoatings.com/top-benefits-of-integrating-a-data-management-system-in-your-powder-coating-line.html
[4] https://patents.google.com/patent/CN111566648B/zh
[5] https://www.keenesystems.com/blog/7-ways-smart-data-management-will-transform-your-manufacturing-profits
[6] https://patents.google.com/patent/CN1985253A
[7] https://signum-solutions.co.uk/real-time-data-analysis-in-manufacturing/
[8] https://patents.google.com/patent/CN111209363A/zh
[9] https://www.elcometerusa.com/Digital-Data-Management-for-Coating-Inspection-Tasks-on-Steel-Structures.html
[10] https://www.academia.edu/44987396/%E8%B0%B7%E6%AD%8C%E4%BC%98%E5%8C%96
Hot Tags: China, Global, OEM, private label, manufacturers, factory, suppliers, manufacturing company