Content Menu
● Understanding Powder Coating and Its Challenges
● What Is a Smart Data Management System in Powder Coating?
>> Key Components of a Smart Data Management System
● How Smart Data Management Enhances Powder Coating Efficiency
>> 1. Optimized Powder Usage
>> 2. Consistent Coating Quality
>> 3. Reduced Downtime Through Predictive Maintenance
>> 4. Improved Process Transparency and Control
>> 5. Integration with Factory Systems
● Implementing a Smart Data Management System: Best Practices
>> Assess Your Current Process
>> Choose the Right System
>> Train Your Team
>> Monitor and Optimize Continuously
● Case Study: Smart Data Management in Action
● Future Trends in Powder Coating Efficiency
● Frequently Asked Questions (FAQs)
Powder coating is a widely used finishing process in industries ranging from automotive to appliances, prized for its durability, environmental friendliness, and aesthetic appeal. However, achieving optimal efficiency in powder coating operations requires more than just quality materials and skilled labor—it demands intelligent control and data-driven management. This article explores how integrating a smart data management system can revolutionize powder coating efficiency, reduce waste, and enhance product quality.
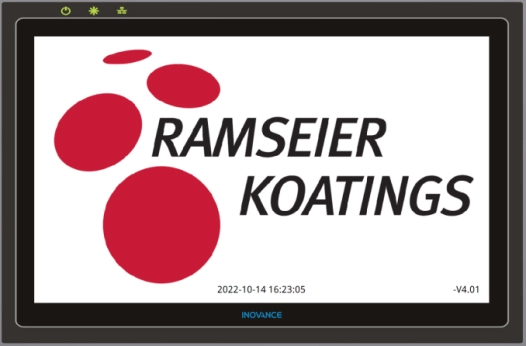
Understanding Powder Coating and Its Challenges
Powder coating involves applying a dry powder to a surface electrostatically and then curing it under heat to form a durable finish. Despite its advantages, powder coating processes face several challenges:
- Material Waste: Overspray and inconsistent application can lead to significant powder loss.
- Process Variability: Manual adjustments and lack of real-time monitoring can cause uneven coatings.
- Maintenance Downtime: Unexpected equipment failures disrupt production and increase costs.
- Data Silos: Lack of integrated data makes it difficult to analyze and optimize the entire coating process.
Addressing these challenges requires a system that not only controls the coating application but also collects, analyzes, and acts on data in real time.
What Is a Smart Data Management System in Powder Coating?
A smart data management system for powder coating is a digital platform that integrates with coating equipment to collect, store, and analyze operational data. It enables operators and managers to monitor key parameters, optimize settings, and predict maintenance needs.
Key Components of a Smart Data Management System
- Centralized Control Interface: Modern controllers like Gema's MagicControl 4.0 or Nordson's Encore Engage provide intuitive touchscreens that centralize control over guns, conveyors, and booths.
- Real-Time Data Acquisition: Sensors and connected devices continuously monitor parameters such as powder flow rate, electrostatic charge, conveyor speed, and environmental conditions.
- Data Analytics and Visualization: The system processes collected data to display performance metrics, detect anomalies, and generate actionable insights.
- Network Connectivity: Ethernet and CanBus protocols enable seamless communication between system components and integration with higher-level factory management systems.
- Predictive Maintenance: By analyzing trends and patterns, the system can forecast equipment wear and schedule maintenance before failures occur.
How Smart Data Management Enhances Powder Coating Efficiency
1. Optimized Powder Usage
Smart systems allow precise control of powder application parameters. Operators can adjust flow rates and electrostatic settings for individual guns or groups, minimizing overspray and powder waste. For example, Nordson's dense-phase technology combined with smart controllers has demonstrated powder savings of up to 30% compared to traditional venturi pump systems.
2. Consistent Coating Quality
By monitoring coating thickness and environmental conditions, the system ensures uniform application. Automated recipe management enables quick switching between product specifications without manual recalibration, reducing variability and rework.
3. Reduced Downtime Through Predictive Maintenance
Real-time monitoring of equipment health allows early detection of wear or faults. Predictive maintenance scheduling based on this data prevents unexpected breakdowns, extending machinery life and maintaining production continuity.
4. Improved Process Transparency and Control
Operators gain full visibility of the coating line's status on a single screen, including alerts and maintenance timers. Video tutorials and guided workflows reduce training time and operator errors, leading to higher productivity.
5. Integration with Factory Systems
Smart data management systems can link with enterprise resource planning (ERP) and manufacturing execution systems (MES), enabling holistic production management and better decision-making.
Implementing a Smart Data Management System: Best Practices
Assess Your Current Process
Begin by evaluating your existing powder coating setup, including equipment capabilities, process bottlenecks, and quality issues. Identify key performance indicators (KPIs) such as powder consumption, coating uniformity, and downtime frequency.
Choose the Right System
Select a system that matches your operational scale and requirements. Options range from entry-level controllers to premium solutions with full automation and extensive data analytics capabilities. Consider compatibility with your current equipment and future scalability.
Train Your Team
Ensure operators and maintenance staff are trained to use the new system effectively. Leverage built-in tutorials and user-friendly interfaces to minimize the learning curve.
Monitor and Optimize Continuously
Use the system's data insights to refine process parameters regularly. Implement predictive maintenance schedules and adjust recipes based on product feedback and environmental changes.
Case Study: Smart Data Management in Action
A manufacturing plant upgraded its powder coating line with a smart control system featuring a centralized touchscreen interface and real-time data analytics. The results included:
- 25% reduction in powder consumption due to optimized gun settings.
- 15% increase in throughput by minimizing downtime with predictive maintenance.
- Consistent coating thickness within ±10 microns, improving product durability.
- Enhanced operator confidence and reduced training time thanks to intuitive controls.
This example highlights the tangible benefits of integrating smart data management in powder coating operations.
Future Trends in Powder Coating Efficiency
Emerging technologies promise to further enhance powder coating efficiency:
- Artificial Intelligence (AI): AI algorithms can analyze vast datasets to optimize coating recipes and predict failures with higher accuracy.
- IoT Integration: Internet of Things devices enable even more granular data collection and remote monitoring.
- Smart Coatings: Development of coatings with embedded sensors for real-time wear and damage monitoring is underway, offering new dimensions of quality control.
Frequently Asked Questions (FAQs)
Q1: What is the main advantage of using a smart data management system in powder coating?
A1: It significantly improves efficiency by optimizing powder usage, ensuring consistent quality, reducing downtime through predictive maintenance, and providing comprehensive process control.
Q2: Can smart data management systems be integrated with existing powder coating equipment?
A2: Yes, many systems are designed to retrofit existing lines and can be customized to meet specific operational needs.
Q3: How does predictive maintenance work in these systems?
A3: The system collects real-time data on equipment performance and uses analytics to identify patterns indicating potential failures, allowing maintenance to be scheduled proactively.
Q4: Are these systems user-friendly for operators?
A4: Modern systems feature intuitive touchscreens, guided workflows, and video tutorials to facilitate easy operation and reduce training time.
Q5: What kind of cost savings can be expected from implementing a smart data management system?
A5: Savings come from reduced powder waste (up to 30%), lower maintenance costs due to fewer breakdowns, improved throughput, and less rework from quality issues.
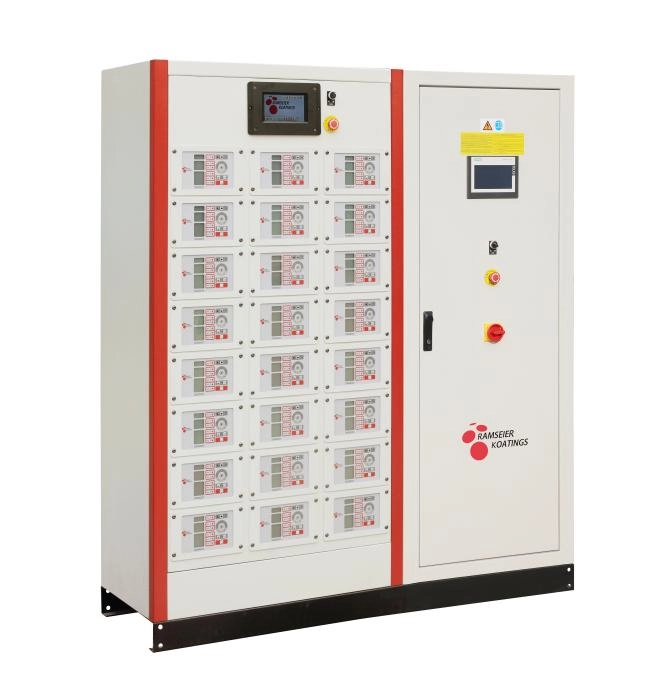
[1] https://www.wagner-group.com/us/industry/products/powder-coating/complete-systems/
[2] https://huggingface.co/facebook/xm_transformer_unity_en-hk/raw/main/en_zh_spm.dict
[3] https://www.gemapowdercoating.com/en/products/automatic-equipment-and-guns/magiccontrol-40
[4] https://www.cs.cmu.edu/afs/cs.cmu.edu/project/cmt-40/Nice/Transfer/Chinese/xferlexicon.txt
[5] https://www.youtube.com/watch?v=KSCa1y-Rx98
[6] https://huggingface.co/openbmb/cpm-bee-1b/commit/bd72a61dd7a59086ed7456f1dfcaa995c8ec58a3.diff
[7] https://www.nordson.com/en/products/industrial-coating-systems-products/powder-coating-control-systems
[8] https://www.ramseierkoatings.com/why-a-smart-data-management-system-is-essential-for-modern-coating-lines.html
[9] https://www.ramseierkoatings.com/why-powder-coating-manufacturers-are-switching-to-smart-data-management-systems.html
[10] https://www.bolair.ca/blog/smart-technologies-powder-coating/
Hot Tags: China, Global, OEM, private label, manufacturers, factory, suppliers, manufacturing company