Content Menu
● Understanding Traditional Control Systems
>> What Are Traditional Control Systems?
>> Key Features of Traditional Control Systems
● What Is a Data Management System?
>> Defining Data Management Systems in Industrial Context
>> Core Capabilities of a DMS
● Comparing Control Systems and Data Management Systems for Spray Lines
>> Spray Line Requirements
>> Control Performance
>> Data Insight and Optimization
>> Integration and Scalability
● Advantages of Data Management Systems Over Traditional Control Systems
● Challenges and Considerations
>> Complexity and Cost
>> Real-time Control Dependence
>> Data Quality and Integrity
● Case Study: Spray Line Application with PWM Control and DMS Integration
● Making the Right Choice for Your Spray Line
>> When to Choose Traditional Control Systems
>> When to Invest in a Data Management System
● Conclusion
● Frequently Asked Questions (FAQs)
In modern industrial operations, especially in spray line management, choosing the right control and data handling system is crucial for optimizing performance, efficiency, and product quality. Traditional control systems have long been the backbone of process automation, while data management systems (DMS) represent a newer, more integrated approach leveraging real-time data analytics and visualization. This article explores both systems in depth, comparing their functionalities, benefits, and challenges to help you decide which is better suited for your spray line.
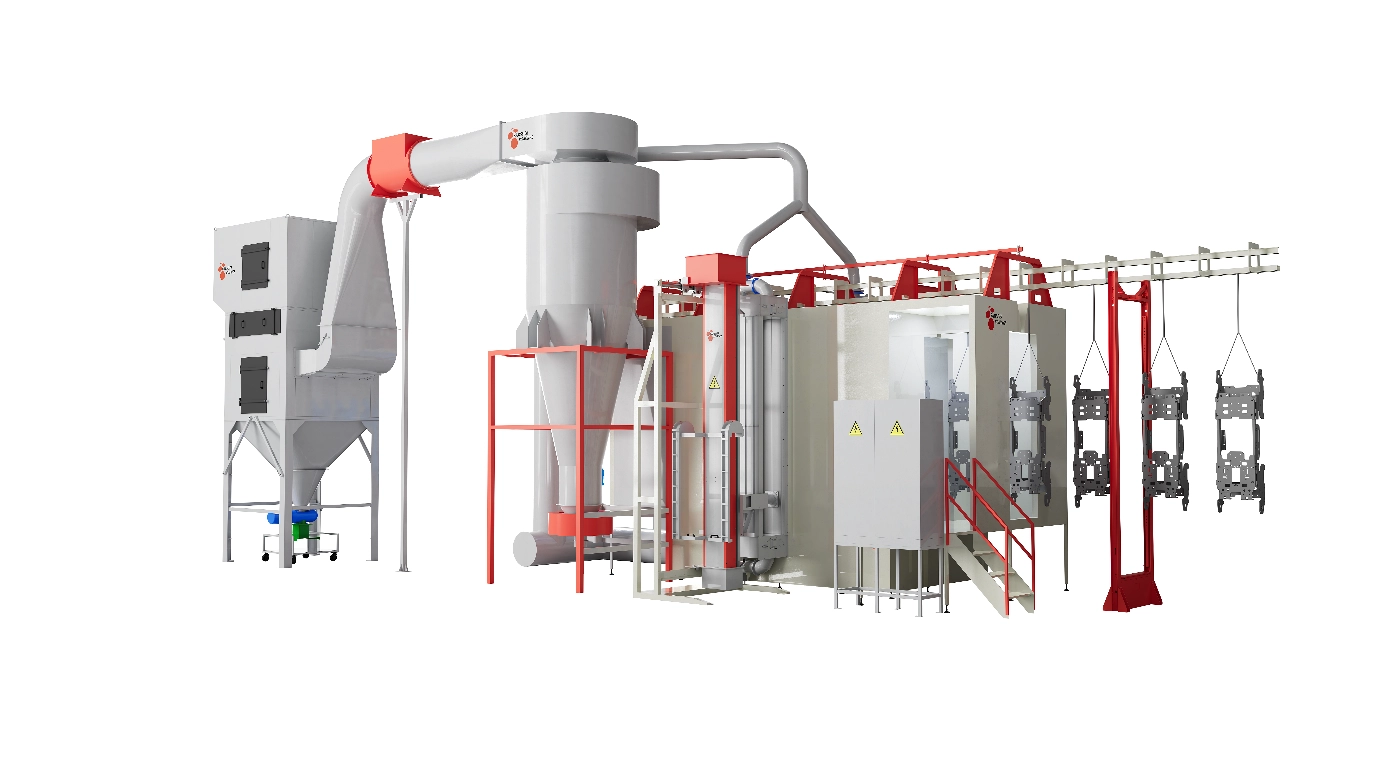
Understanding Traditional Control Systems
What Are Traditional Control Systems?
Traditional control systems typically refer to Programmable Logic Controllers (PLCs), Distributed Control Systems (DCS), or relay-based automation that manage industrial processes through predefined logic and real-time control loops. These systems directly monitor inputs from sensors, execute control algorithms, and send commands to actuators to regulate operations such as spray rates, pressure, and flow.
Key Features of Traditional Control Systems
- Real-time process control: They provide immediate response to sensor inputs to maintain process variables within set parameters.
- Deterministic operation: Control logic is fixed and predictable, ensuring stable and reliable process execution.
- Robustness: Designed for harsh industrial environments with high reliability and uptime.
- Limited data handling: Primarily focused on control; data collection and analysis are often secondary or require separate systems.
What Is a Data Management System?
Defining Data Management Systems in Industrial Context
A Data Management System (DMS) is an integrated software platform that collects, cleanses, stores, enriches, and visualizes real-time operational data from various sources within an industrial environment. Unlike traditional control systems, DMS focuses on managing data flow and providing actionable insights through analytics, enabling better decision-making and process optimization.
Core Capabilities of a DMS
- Data collection from multiple sources: Supports vendor-neutral connectivity to various sensors, IIoT devices, and control systems.
- Data contextualization and visualization: Provides dynamic dashboards and asset frameworks to view data in operational context.
- Secure and reliable data delivery: Ensures data integrity with buffering, failover, and high availability.
- Edge-to-cloud scalability: Enables data processing at the edge, on-premises, or cloud, depending on operational needs.
- Integration with analytics and AI: Facilitates rapid data transfer to business intelligence tools for advanced analysis.
Comparing Control Systems and Data Management Systems for Spray Lines
Spray Line Requirements
Spray lines require precise control of application rates, pressure, and timing to ensure uniform coating and minimize waste. Additionally, modern spray lines benefit from detailed data analysis to optimize performance, detect anomalies, and support maintenance.
Control Performance
Traditional control systems excel at real-time, deterministic control of spray line actuators and valves. They ensure that the spray rate is maintained within tight tolerances, responding immediately to sensor feedback. For example, pulse width modulation (PWM) controllers in spray systems have demonstrated faster response times and more precise rate control compared to older rate controllers, enabling better site-specific applications even in small zones.
Data Insight and Optimization
Data Management Systems provide comprehensive data handling and visualization capabilities that traditional control systems lack. By aggregating operational data, DMS platforms enable operators and managers to:
- Identify trends and inefficiencies.
- Predict maintenance needs.
- Optimize spray parameters based on historical and real-time data.
- Support sustainability goals by reducing overspray and chemical usage.
Integration and Scalability
While traditional control systems are often limited to controlling specific equipment or processes, DMS platforms offer scalable integration across multiple spray lines, plants, or even enterprise-wide operations. This allows centralized monitoring and data-driven decision-making at higher organizational levels.
Advantages of Data Management Systems Over Traditional Control Systems
Aspect | Data Management System (DMS) | Traditional Control System |
Data Handling | Collects, stores, and visualizes large volumes of data in real time | Limited data collection, mainly control-focused |
Decision Support | Provides analytics, predictive insights, and reporting | Relies on operator interpretation of control data |
Flexibility | Vendor-neutral, supports multiple protocols and devices | Often vendor-specific and siloed |
Scalability | Easily scales from edge to cloud and across multiple sites | Typically constrained to local control loops |
User Access | Self-service dashboards accessible remotely via web/mobile | Localized control panels with limited remote access |
Maintenance | Enables predictive maintenance through data trends | Mostly reactive maintenance based on alarms |
Challenges and Considerations
Complexity and Cost
Implementing a DMS requires investment in software, infrastructure, and training. The complexity of integrating diverse data sources and ensuring cybersecurity can be significant compared to traditional control systems, which are often simpler and well-understood.
Real-time Control Dependence
DMS platforms generally do not replace real-time control hardware but complement it. Spray lines still need reliable control systems to execute immediate commands, while DMS provides the data backbone for optimization.
Data Quality and Integrity
Maintaining clean and reliable data streams is critical. DMS solutions incorporate buffering and failover mechanisms to prevent data loss, but poor sensor calibration or network issues can still affect data quality.
Case Study: Spray Line Application with PWM Control and DMS Integration
Recent studies comparing Pulse Width Modulation (PWM) sprayer controllers with traditional rate controllers (RC) show PWM systems achieve faster and more precise application rate adjustments. When combined with a DMS that collects and analyzes operational data, the spray line can:
- Quickly adapt to variable rate prescriptions.
- Minimize misapplication in small spray zones.
- Provide real-time feedback to operators via dashboards.
- Enable data-driven adjustments to improve efficiency and reduce chemical use.
This synergy between advanced control and data management exemplifies the future of spray line operations.
Making the Right Choice for Your Spray Line
When to Choose Traditional Control Systems
- If your primary need is reliable, real-time control with minimal complexity.
- When operating in environments with limited IT infrastructure.
- For smaller-scale operations where detailed data analytics are not critical.
When to Invest in a Data Management System
- If optimizing spray line efficiency and sustainability is a priority.
- When managing multiple spray lines or facilities requiring centralized monitoring.
- To leverage predictive maintenance and advanced analytics.
- If integrating with enterprise-level business intelligence tools is desired.
Conclusion
Both traditional control systems and data management systems play vital roles in spray line operations. Traditional control systems provide the essential real-time control needed for precise spraying, while data management systems offer a broader, strategic view that enables optimization, predictive maintenance, and scalability. For modern spray lines aiming for efficiency, sustainability, and data-driven decision-making, integrating a robust data management system alongside reliable control hardware represents the best approach.
Frequently Asked Questions (FAQs)
Q1: Can a Data Management System replace a traditional control system on a spray line?
A1: No, a DMS complements but does not replace real-time control hardware. Control systems are necessary for immediate process regulation, while DMS focuses on data collection and analysis.
Q2: What benefits does PWM control offer compared to traditional rate controllers?
A2: PWM controllers respond faster and more precisely to rate changes, enabling accurate application even in small spray zones, reducing waste and improving efficiency.
Q3: How does a Data Management System improve maintenance on a spray line?
A3: By analyzing operational data trends, a DMS can predict equipment failures before they occur, enabling proactive maintenance and reducing downtime.
Q4: Is it difficult to integrate a DMS with existing spray line equipment?
A4: Modern DMS platforms are designed to be vendor-neutral and support multiple protocols, easing integration with a wide range of existing equipment.
Q5: What are the cost implications of implementing a Data Management System?
A5: Initial costs include software, hardware, and training. However, these investments often pay off through improved efficiency, reduced waste, and lower maintenance costs over time.
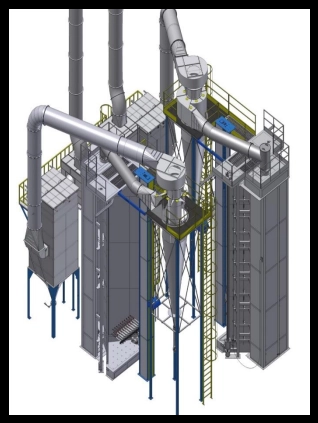
[1] https://www.aveva.com/en/products/aveva-pi-system/
[2] https://patents.google.com/patent/CN106021209A/zh
[3] https://www.mdpi.com/2624-7402/6/3/189
[4] https://patents.google.com/patent/CN107526766A/zh
[5] https://ieeecss.org/sites/ieeecss/files/2019-07/IoCT-FullReport_v2.pdf
[6] https://patents.google.com/patent/CN1985253A
[7] https://www.ramseierkoatings.com/data-management-system-vs-traditional-control-systems-which-is-better-for-your-powder-coating-line.html
[8] https://patents.google.com/patent/CN111566648B/zh
[9] https://www.ramseierkoatings.com/data-management-system-vs-plc-control-which-offers-better-insights-and-efficiency.html
[10] https://blog.csdn.net/sykalon/article/details/141163430
Hot Tags: China, Global, OEM, private label, manufacturers, factory, suppliers, manufacturing company