Content Menu
● Understanding Real-Time Data Management in Powder Coating
>> What Is a Real-Time Data Management System?
>> Key Components of the System
● Major Benefits of Real-Time Data Management Systems in Powder Coating
>> Enhanced Process Control and Quality Assurance
>> Increased Operational Efficiency
>> Improved Inventory and Cost Management
>> Predictive Maintenance and Reduced Downtime
>> Enhanced Reporting and Decision-Making
● How Real-Time Data Management Transforms Powder Coating Operations
>> Streamlining Batch Powder Coating Systems
>> Facilitating Traceability and Compliance
>> Supporting Workforce Efficiency
● Challenges Addressed by Real-Time Data Management
● Future Trends and Innovations
● Frequently Asked Questions
Powder coating is a critical finishing process used widely in industries such as automotive, metal furniture, renewable energy, and infrastructure due to its durability, corrosion resistance, and aesthetic appeal. The complexity and precision required in powder coating processes demand robust management tools to ensure quality, efficiency, and cost-effectiveness. A real-time data management system has emerged as a transformative solution, offering numerous benefits that enhance the entire powder coating workflow from surface preparation to final inspection.
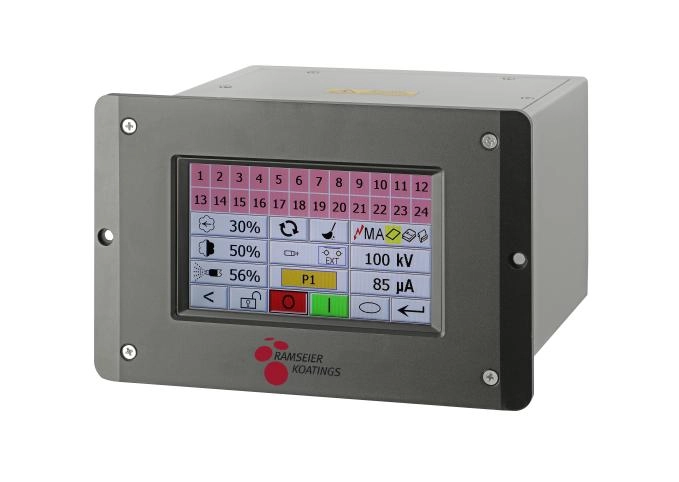
Understanding Real-Time Data Management in Powder Coating
What Is a Real-Time Data Management System?
A real-time data management system in powder coating is an integrated software platform that continuously collects, processes, and displays data generated throughout the coating process. This includes parameters such as temperature, voltage, curing time, powder usage, machine status, and quality inspection results. By providing instantaneous visibility into every step, the system enables operators and managers to make informed decisions promptly.
Key Components of the System
- Data Acquisition Devices: Sensors and measurement tools capture process variables.
- Centralized Software Platform: Aggregates and analyzes data in real time.
- User Interface: Visual dashboards and alerts for operators and supervisors.
- Integration Capabilities: Connects with ERP, MES, and SCADA systems for seamless workflow management.
Major Benefits of Real-Time Data Management Systems in Powder Coating
Enhanced Process Control and Quality Assurance
One of the most significant advantages of using real-time data management is the ability to maintain stringent quality standards. The system continuously monitors critical parameters such as coating thickness, curing temperature, and powder application rates. Any deviation from preset thresholds triggers immediate alerts, allowing operators to correct issues before they escalate.
This proactive control reduces defects, minimizes rework, and ensures consistent coating quality across batches. Moreover, automated data logging creates a comprehensive audit trail, simplifying compliance with industry regulations and customer specifications.
Increased Operational Efficiency
Real-time data visibility enables better scheduling and resource allocation. Managers can track job progress, machine availability, and inventory levels instantaneously, which helps optimize workflow and reduce downtime. For example, by batching orders with similar powder colors or process requirements, the system maximizes throughput while minimizing changeover times.
Additionally, automated instructions for racking and packing reduce human errors and streamline handling processes. This leads to smoother operations and faster turnaround times.
Improved Inventory and Cost Management
Integrating inventory management with real-time data allows powder coaters to monitor powder consumption and raw material usage precisely. The system updates inventory levels dynamically as jobs progress, ensuring accurate stock control and preventing shortages or overstocking.
Cost tracking tied to specific jobs or racks helps identify profitability at a granular level. Businesses can adjust pricing strategies based on actual labor and material costs, improving financial performance.
Predictive Maintenance and Reduced Downtime
Real-time monitoring of equipment performance helps identify wear patterns and potential failures before they cause unplanned downtime. Predictive maintenance alerts generated by the system enable maintenance teams to schedule repairs proactively, reducing costly breakdowns and extending equipment lifespan.
This data-driven approach to maintenance ensures continuous production flow and lowers overall operational risks.
Enhanced Reporting and Decision-Making
Automated reporting features provide instant access to production metrics, quality data, and financial summaries without manual effort. Managers and owners can view real-time dashboards or generate detailed reports on demand, facilitating quicker and more accurate decision-making.
This transparency improves communication across departments and with customers, enhancing trust and satisfaction.
How Real-Time Data Management Transforms Powder Coating Operations
Streamlining Batch Powder Coating Systems
Batch powder coating processes benefit greatly from automation and data integration. Real-time systems synchronize application robots, machine vision inspection, and parameter control software to deliver uniform coatings with minimal defects. Operators receive immediate feedback on surface preparation quality and curing conditions, ensuring every batch meets specifications.
Facilitating Traceability and Compliance
Traceability is essential in powder coating to verify that every product meets quality and safety standards. Real-time data systems link process data to specific parts, racks, or orders, enabling full traceability from raw material to finished product. This capability is invaluable during audits or when addressing customer complaints.
Supporting Workforce Efficiency
By providing clear, step-by-step instructions for each job, including racking and packing details, the system reduces training time and errors for new or temporary employees. Real-time visibility into individual employee performance also helps managers allocate tasks effectively and identify areas for improvement.
Challenges Addressed by Real-Time Data Management
- Reducing Waste: Optimized powder application minimizes excess powder usage, lowering material costs and environmental impact.
- Avoiding Bottlenecks: Instant alerts and workflow visualization help identify and resolve production slowdowns.
- Maintaining Consistency: Automated control ensures uniform application and curing, reducing variability.
- Meeting Deadlines: Dynamic scheduling based on real-time data ensures jobs are completed on time without overloading resources.
Future Trends and Innovations
The integration of real-time data management with advanced analytics and artificial intelligence promises even greater improvements. Predictive models can forecast equipment failures, optimize process parameters, and suggest operational adjustments automatically. Cloud-based platforms enable remote monitoring and collaboration, expanding the reach of these systems beyond the plant floor.
Frequently Asked Questions
1. How does a real-time data management system improve powder coating quality?
It continuously monitors key process parameters and alerts operators to deviations, enabling immediate corrections that ensure consistent, high-quality finishes.
2. Can the system help reduce powder waste?
Yes, by tracking powder usage and application rates, it helps optimize material consumption, reducing waste and lowering costs.
3. Is real-time data management compatible with existing ERP systems?
Most modern systems are designed for integration with ERP, MES, and SCADA platforms, allowing seamless data exchange and unified process control.
4. How does predictive maintenance work in these systems?
The system analyzes equipment performance data to identify patterns indicating potential failures, triggering maintenance alerts before breakdowns occur.
5. What industries benefit most from real-time data management in powder coating?
Industries requiring high-quality, durable finishes such as automotive, renewable energy, metal furniture, and infrastructure gain significant advantages.
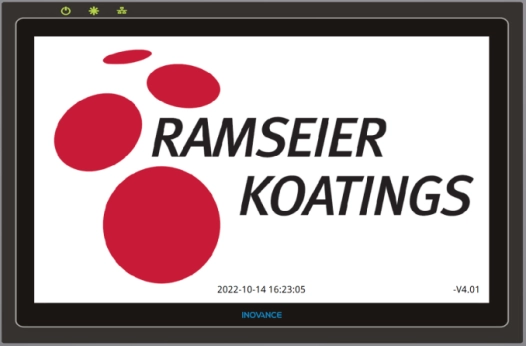
[1] https://inspenet.com/en/articulo/batch-powder-coating-system-fundamentals/
[2] https://ia800600.us.archive.org/5/items/ittushu-2470/%E6%B8%85%E5%8D%8E%E5%A4%A7%E5%AD%A6%E5%9B%BE%E4%B9%A6%E9%A6%86-%E6%88%98%E7%96%AB%E7%89%88/H_%E8%AF%AD%E8%A8%80%E3%80%81%E6%96%87%E5%AD%97/12133_%E5%9B%BD%E9%99%85%E4%BA%A4%E6%B5%81%E8%8B%B1%E8%AF%AD%E9%98%85%E8%AF%BB%E8%BF%9B%E9%98%B6%E6%95%99%E7%A8%8B_text.pdf
[3] https://gosteelhead.com/powder-coating-software
[4] https://huggingface.co/facebook/xm_transformer_unity_hk-en/commit/e37fd5ab9c6faf7a9547972cf6dace1c144c49c8.diff?file=en_zh_spm.dict
[5] https://proplate.pro/powder-coating/
[6] https://www.scribd.com/document/498929761/%E5%8F%8C%E8%89%B2%E8%A1%A8%E8%A7%A3%E8%8B%B1%E8%AF%AD%E8%AF%8D%E6%B1%87
[7] https://proplate.pro/how-powder-coating-manufacturers-can-boost-erp-efficiency/
[8] https://mdx.mdict.org/%E6%8C%89%E8%AF%8D%E5%85%B8%E8%AF%AD%E7%A7%8D%E6%9D%A5%E5%88%86%E7%B1%BB/%E8%8B%B1%E8%AF%AD/%E8%8B%B1%E8%AF%AD%E4%B8%93%E4%B8%9A%E8%AF%8D%E5%85%B8/%5B%E8%8B%B1-%E6%B1%89%5D/%5B%E8%8B%B1-%E6%B1%89%5D%206%E4%B8%87%E5%A4%9A%E4%B8%AA%E5%8F%A5%E5%AD%90%E9%A3%9E%E8%B7%836.0%E5%8F%A5%E5%BA%93%E5%AF%BC%E5%87%BA%EF%BC%88%E9%99%84%E6%BA%90%E6%96%87%E4%BB%B6%EF%BC%89/%5B%E8%8B%B1-%E6%B1%89%5D%206%E4%B8%87%E5%A4%9A%E4%B8%AA%E5%8F%A5%E5%AD%90%E9%A3%9E%E8%B7%836.0%E5%8F%A5%E5%BA%93%E5%AF%BC%E5%87%BA%EF%BC%88%E9%99%84%E6%BA%90%E6%96%87%E4%BB%B6%EF%BC%89.txt
[9] https://www.ramseierkoatings.com/top-benefits-of-integrating-a-data-management-system-in-your-powder-coating-line.html
[10] https://www.scribd.com/document/674645326/%E6%9F%AF%E6%9E%97%E6%96%AF%E8%8B%B1%E8%AF%AD%E8%AF%AD%E6%B3%95%E7%B3%BB%E5%88%97-1-%E4%BB%8B%E8%AF%8D
Hot Tags: China, Global, OEM, private label, manufacturers, factory, suppliers, manufacturing company