Content Menu
● Understanding Automatic Spray Booths and Their Data Needs
>> Why Data Management is Critical
● Key Features of an Ideal Data Management System for Automatic Spray Booths
>> 1. Seamless Integration with Booth Hardware and Software
>> 2. Real-Time Monitoring and Alerts
>> 3. Comprehensive Data Logging and Reporting
>> 4. Predictive Maintenance and Efficiency Optimization
>> 5. User-Friendly Interface and Accessibility
>> 6. Compliance with Industry Standards and Safety Regulations
● Technical Considerations for Implementing a Data Management System
>> H2: Data Security and Privacy
>> H3: Scalability and Flexibility
>> H3: Interoperability with Existing Systems
● Benefits of an Ideal Data Management System for Automatic Spray Booths
● Frequently Asked Questions (FAQs)
Automatic spray booths have revolutionized industrial painting by enhancing efficiency, consistency, and safety. However, the backbone of these sophisticated systems is a robust data management system (DMS) that ensures seamless operation, monitoring, and maintenance. This article explores the essential characteristics that make a data management system ideal for automatic spray booths, emphasizing integration, real-time monitoring, data analytics, compliance, and user accessibility.
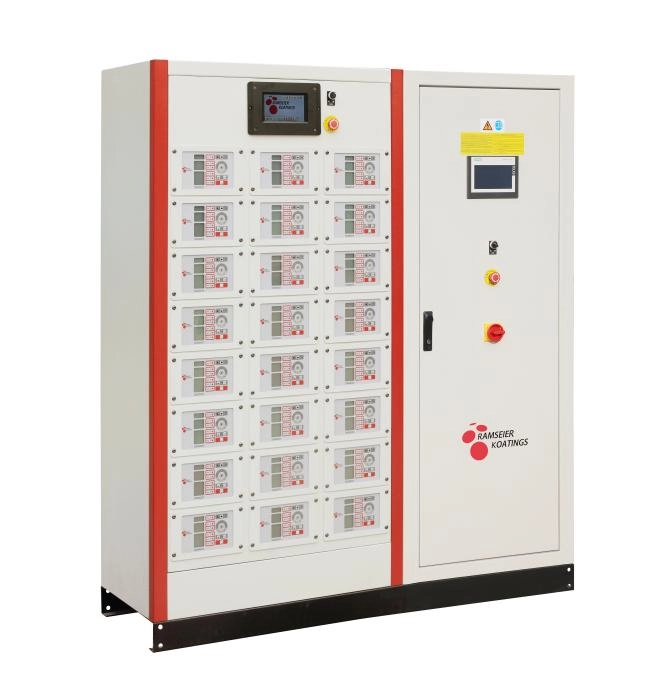
Understanding Automatic Spray Booths and Their Data Needs
Automatic spray booths are enclosed environments where paint or coatings are applied to products using automated spray equipment. These booths require precise control over environmental factors such as airflow, temperature, humidity, and filtration to ensure high-quality finishes and operator safety.
Why Data Management is Critical
The complexity of automatic spray booths demands continuous monitoring and control of numerous parameters. A data management system collects, organizes, analyzes, and reports this information, enabling operators and managers to optimize performance, ensure safety, and maintain regulatory compliance.
Key Features of an Ideal Data Management System for Automatic Spray Booths
1. Seamless Integration with Booth Hardware and Software
An ideal DMS must integrate effortlessly with various spray booth components, including sensors, control panels, and automated spray equipment. This integration allows the system to collect comprehensive data on booth pressure, filter status, burner operation, temperature, humidity, and more.
Modern solutions, such as Booth Connect from Global Finishing Solutions (GFS), exemplify this by monitoring multiple parameters for booths from different manufacturers without requiring an onsite server. Data is securely stored in the cloud, enabling flexible and scalable integration across diverse booth portfolios.
2. Real-Time Monitoring and Alerts
Real-time visibility into spray booth operations is essential for maintaining optimal conditions and preventing downtime. The DMS should provide continuous updates on critical metrics such as airflow, filter loading, temperature, and energy consumption.
Advanced systems feature dashboards accessible via computers, tablets, or smartphones, allowing painters, managers, and owners to monitor booth performance remotely. Notifications and alarms can alert users immediately if the booth enters an alarm state or if connectivity is lost, enabling swift corrective actions to protect equipment and maintain production flow.
3. Comprehensive Data Logging and Reporting
Accurate and detailed data logging is fundamental to understanding booth performance over time. The system should record environmental conditions, operational cycles, maintenance activities, and energy usage at specified intervals.
With this data, operators can generate comprehensive reports that reveal trends, identify anomalies, and benchmark performance against industry standards. These insights facilitate process optimization, ensure compliance with safety and environmental regulations, and support proactive maintenance planning to reduce unexpected breakdowns.
4. Predictive Maintenance and Efficiency Optimization
An ideal DMS leverages data analytics to predict maintenance needs before failures occur. For example, monitoring filter loading trends helps determine the optimal time for filter replacement, preventing damage to ductwork or fans and avoiding unnecessary downtime.
By analyzing energy consumption and operational patterns, the system can also suggest adjustments to improve efficiency, reduce resource waste, and lower operating costs. This proactive approach enhances the longevity of booth components and maximizes production uptime.
5. User-Friendly Interface and Accessibility
The data management system should offer an intuitive interface that caters to various users, from on-floor operators to corporate decision-makers. Customizable dashboards and reports allow users to focus on relevant metrics and make informed decisions quickly.
Cloud-based storage and mobile access ensure that critical data and alerts are available anytime and anywhere, facilitating timely interventions and strategic planning across multiple locations or facilities.
6. Compliance with Industry Standards and Safety Regulations
Spray booths operate under strict regulatory frameworks to ensure environmental safety and worker health. An ideal DMS supports compliance with standards set by organizations such as OSHA, NFPA, EPA, and ICC.
The system should track parameters related to volatile organic compounds (VOCs), particulate matter, ventilation rates, and electrical safety, generating documentation required for audits and inspections. Automated alerts for deviations help maintain safe operating conditions consistently.
Technical Considerations for Implementing a Data Management System
H2: Data Security and Privacy
Given the sensitive nature of operational data, the DMS must employ robust security measures, including encryption and secure cloud storage, to protect against unauthorized access and data breaches. Zero-knowledge encryption techniques can ensure that data stored on remote servers remains confidential.
H3: Scalability and Flexibility
The system should accommodate growth and changes in production demands. Whether managing a single booth or an entire portfolio across multiple sites, the DMS must scale without compromising performance or usability.
H3: Interoperability with Existing Systems
Compatibility with existing enterprise resource planning (ERP), manufacturing execution systems (MES), and other industrial software enhances the value of the DMS by enabling holistic management of production workflows and resource allocation.
Benefits of an Ideal Data Management System for Automatic Spray Booths
- Improved Quality Control: By continuously monitoring environmental and operational parameters, the system helps maintain consistent paint application and finish quality.
- Enhanced Safety: Real-time alerts and compliance tracking reduce risks associated with hazardous materials and equipment malfunctions.
- Operational Efficiency: Data-driven insights enable better scheduling, resource management, and reduced downtime.
- Cost Savings: Predictive maintenance and energy optimization lower operating expenses and extend equipment lifespan.
- Strategic Decision-Making: Comprehensive reporting and portfolio-level dashboards support informed management decisions and continuous improvement initiatives.
Frequently Asked Questions (FAQs)
Q1: How does a data management system improve spray booth maintenance?
A1: By continuously monitoring parameters like filter loading and equipment performance, the system predicts when maintenance is needed, preventing unexpected failures and reducing downtime.
Q2: Can the data management system be accessed remotely?
A2: Yes, modern systems store data securely in the cloud, allowing authorized users to access real-time dashboards and reports from computers, tablets, or smartphones anywhere.
Q3: What kind of data does the system typically collect?
A3: It collects data on booth pressure, temperature, humidity, airflow, filter status, burner operation, energy consumption, and production cycles.
Q4: How does the system help with regulatory compliance?
A4: The system tracks environmental and safety parameters, generates reports for audits, and sends alerts if conditions deviate from regulatory standards, ensuring continuous compliance.
Q5: Is the data management system compatible with booths from different manufacturers?
A5: Many advanced systems are designed for seamless integration with various booth brands and models, providing a unified monitoring platform without requiring onsite servers.
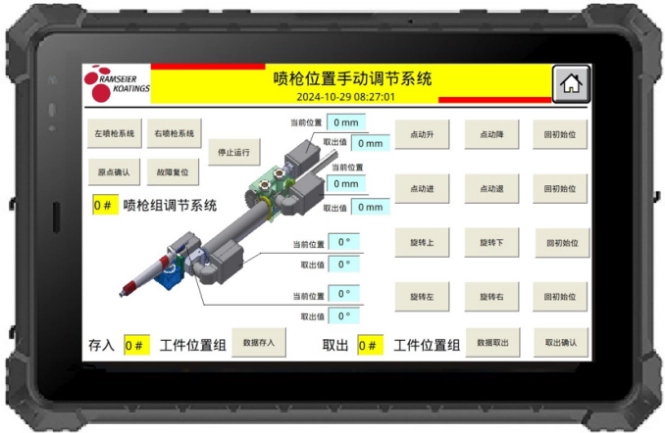
[1] https://www.beacon-equipment.com/gfs.html
[2] https://patents.google.com/patent/CN110717092A/zh
[3] https://globalfinishing.com/products/parts-filters/paint-booth-accessories/booth-connect/
[4] https://patents.google.com/patent/CN111566648B/zh
[5] https://www.sprayboothshop.com/blog/spray-booth-monitoring/
[6] https://patents.google.com/patent/CN1985253A
[7] https://pfsspraybooths.com/how-do-paint-booth-control-panels-work-a-complete-guide
[8] https://www.cnblogs.com/yehong123/p/10576331.html
[9] https://www.spraysystems.com/how-automated-spray-booth-systems-can-save-you-time-and-money/
[10] https://patents.google.com/patent/CN107526766A/zh
Hot Tags: China, Global, OEM, private label, manufacturers, factory, suppliers, manufacturing company