Content Menu
● Understanding the Role of Data Management in Powder Coating
>> What is a Data Management System in Powder Coating?
>> Why is Data Management Critical for Powder Coating Operations?
● Key Factors to Consider When Choosing a Data Management System
>> 1. Compatibility with Powder Coating Equipment
>> 2. Real-Time Monitoring and Alerts
>> 3. Inventory Management Capabilities
>> 4. Process Automation and Workflow Integration
>> 5. Scalability and Customization
>> 6. Cloud-Based Access and Security
● Evaluating System Features and Benefits
>> Dashboard and Reporting Tools
>> Job Costing and Profitability Analysis
>> Compliance and Traceability
>> User-Friendly Interface and Support
● Implementation Considerations
>> Data Migration and Integration
>> Training and Change Management
>> Cost and Return on Investment
● Conclusion
● Frequently Asked Questions
Powder coating is a highly specialized finishing process that demands precision, efficiency, and strict quality control. As powder coating operations grow more complex, managing data from equipment, inventory, and production processes becomes critical to maintaining competitive advantage and operational excellence. Selecting the right data management system (DMS) tailored for powder coating equipment can transform your workflow, improve productivity, and ensure compliance with industry standards.
This article will guide you through the essential considerations and features to evaluate when choosing a data management system for your powder coating equipment.
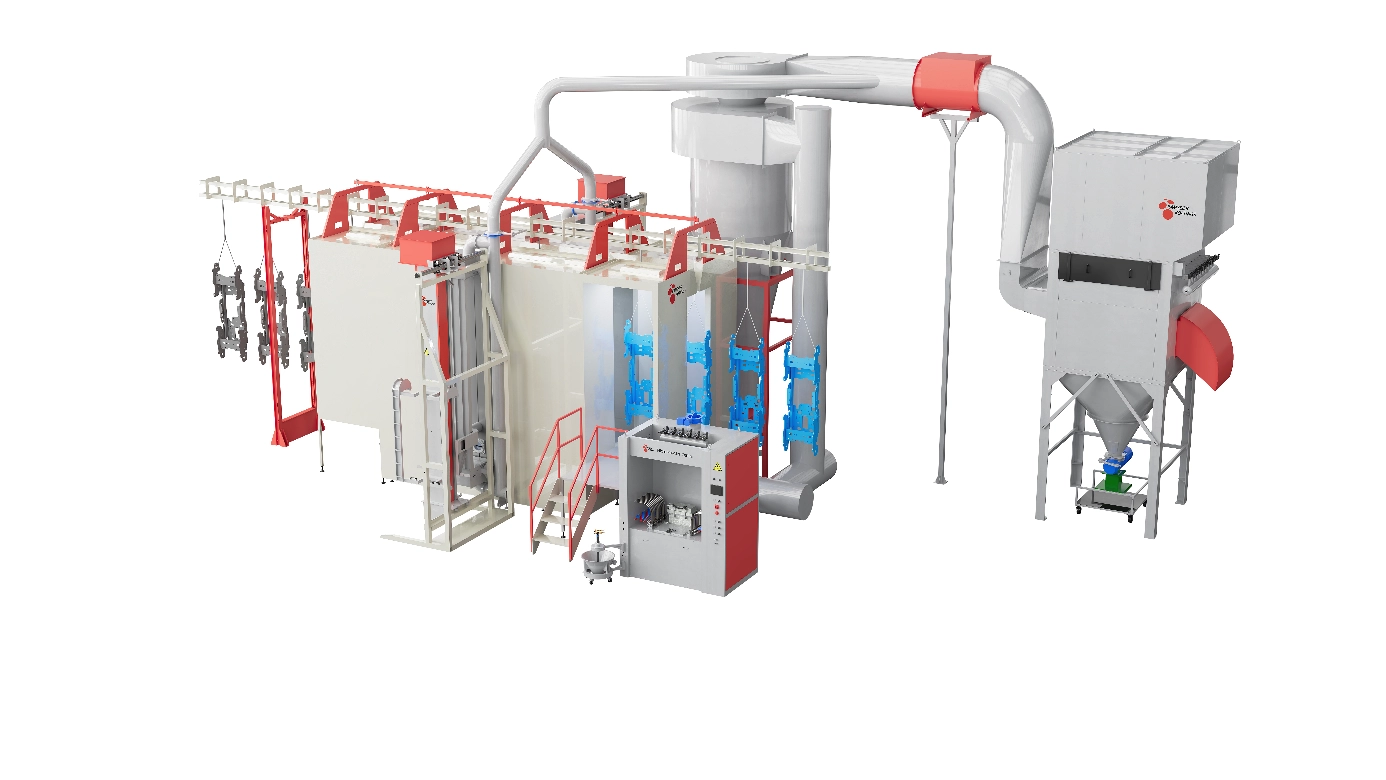
Understanding the Role of Data Management in Powder Coating
What is a Data Management System in Powder Coating?
A data management system for powder coating equipment is a software platform designed to collect, store, analyze, and report data generated during the powder coating process. This includes equipment performance metrics, inventory levels, process parameters, job tracking, and quality indicators.
Effective data management enables real-time monitoring, predictive maintenance, inventory control, and comprehensive reporting, all of which contribute to reduced downtime, improved product quality, and cost savings.
Why is Data Management Critical for Powder Coating Operations?
Powder coating involves multiple variables such as powder type, coating thickness, curing temperature, and equipment settings. Without a robust data system, tracking these variables manually is prone to errors and inefficiencies.
Moreover, compliance with environmental and quality standards (e.g., ISO certifications) requires detailed, retrievable records of chemical usage, batch traceability, and process controls. A DMS automates these tasks, reducing risk and enhancing transparency.
Key Factors to Consider When Choosing a Data Management System
1. Compatibility with Powder Coating Equipment
Your DMS must seamlessly integrate with your existing powder coating hardware, including spray guns, curing ovens, and automation systems. Integration ensures that data flows automatically from equipment sensors to the software platform without manual intervention.
For example, systems like GemaConnect® provide web-based tools that offer full visibility into equipment status and key performance indicators (KPIs) regardless of location or time, enabling multi-level access for business leaders, production staff, and maintenance teams.
2. Real-Time Monitoring and Alerts
Real-time data capture and monitoring allow operators to detect deviations immediately and take corrective actions. Look for systems that provide dashboards with customizable KPIs and alert functions for anomalies such as equipment malfunctions or powder supply shortages.
Predictive maintenance features are especially valuable. Advanced platforms use data analytics to forecast equipment failures before they occur, allowing proactive repairs that minimize downtime and costly breakdowns.
3. Inventory Management Capabilities
Powder coating involves consumables like powders, pretreatment chemicals, and cleaning agents. An effective DMS should include inventory tracking with batch traceability and expiration date monitoring to reduce waste and ensure compliance.
ERP systems tailored for powder coating, such as PROPLATE™, link inventory usage directly to specific jobs, providing granular insight into material consumption and job profitability. This integration helps optimize purchasing and avoid stockouts or overstocking.
4. Process Automation and Workflow Integration
Choose a system that automates routine tasks such as job scheduling, racking and packing instructions, and reporting. Automation reduces human error and frees up staff to focus on value-added activities.
For instance, Steelhead Technologies offers an all-in-one powder coating ERP platform that integrates quoting, production, inventory, and reporting. It supports complex workflows, including batching multiple part numbers on a single rack while maintaining cost tracking and quality control.
5. Scalability and Customization
Your data management needs may evolve as your operation grows or diversifies. Select a system that can scale with your business and be customized to your specific powder coating processes and customer requirements.
Systems like WAGNER's complete powder coating solutions offer different performance classes and modular components, allowing you to tailor the system to your throughput volume, automation level, and quality standards.
6. Cloud-Based Access and Security
Cloud-based DMS platforms provide accessibility from any location and device, facilitating collaboration among departments and remote monitoring. Additionally, cloud solutions often come with robust data security and backup features, protecting your critical production data.
Evaluating System Features and Benefits
Dashboard and Reporting Tools
An intuitive dashboard that visualizes key metrics such as powder usage, equipment uptime, and job progress is essential. Look for customizable views that cater to different roles within your company, from managers to floor operators.
Automated reporting capabilities save time and improve decision-making. Reports on profitability, production efficiency, and compliance can be generated on demand or scheduled regularly.
Job Costing and Profitability Analysis
Linking data on powder consumption, labor time, and equipment usage to individual jobs enables accurate costing and pricing. This insight helps identify profitable jobs and areas for improvement.
Compliance and Traceability
Ensure the system supports regulatory compliance by maintaining detailed logs of chemical usage, batch numbers, and quality checks. Traceability features simplify audits and enhance customer confidence.
User-Friendly Interface and Support
Ease of use is critical for adoption. The system should have a clean interface with minimal training requirements. Additionally, reliable vendor support and training resources are important for smooth implementation and ongoing operation.
Implementation Considerations
Data Migration and Integration
Assess how your current data will be migrated to the new system and how the DMS will integrate with other enterprise systems such as ERP, MES, or quality management software.
Training and Change Management
Successful adoption requires comprehensive training for all users and clear communication about the benefits. Engage stakeholders early and provide ongoing support.
Cost and Return on Investment
Consider upfront costs, subscription fees, and potential savings from improved efficiency, reduced waste, and minimized downtime. A well-chosen DMS can quickly pay for itself through operational improvements.
Conclusion
Choosing the right data management system for your powder coating equipment is a strategic decision that impacts productivity, quality, compliance, and profitability. Prioritize systems that offer seamless equipment integration, real-time monitoring, advanced inventory management, and scalable automation tailored to powder coating processes. Leveraging modern cloud-based platforms with predictive analytics and comprehensive reporting will empower your operation to meet growing demands and maintain a competitive edge.
Frequently Asked Questions
Q1: Why is real-time monitoring important in powder coating data management?
Real-time monitoring allows immediate detection of process deviations or equipment issues, enabling quick corrective actions that prevent defects and downtime.
Q2: How does inventory management in a DMS reduce waste?
By tracking powder and chemical usage with batch and expiration date monitoring, the system ensures materials are used efficiently before they expire, minimizing waste.
Q3: Can a data management system help with regulatory compliance?
Yes, it maintains detailed, retrievable records of chemical usage, batch traceability, and quality checks, simplifying audits and ensuring adherence to standards.
Q4: What role does predictive maintenance play in powder coating equipment management?
Predictive maintenance uses data analytics to forecast equipment failures, allowing proactive repairs that reduce unplanned downtime and costly breakdowns.
Q5: Is cloud-based data management suitable for powder coating operations?
Cloud-based systems offer remote access, enhanced collaboration, data security, and scalability, making them well-suited for modern powder coating businesses.
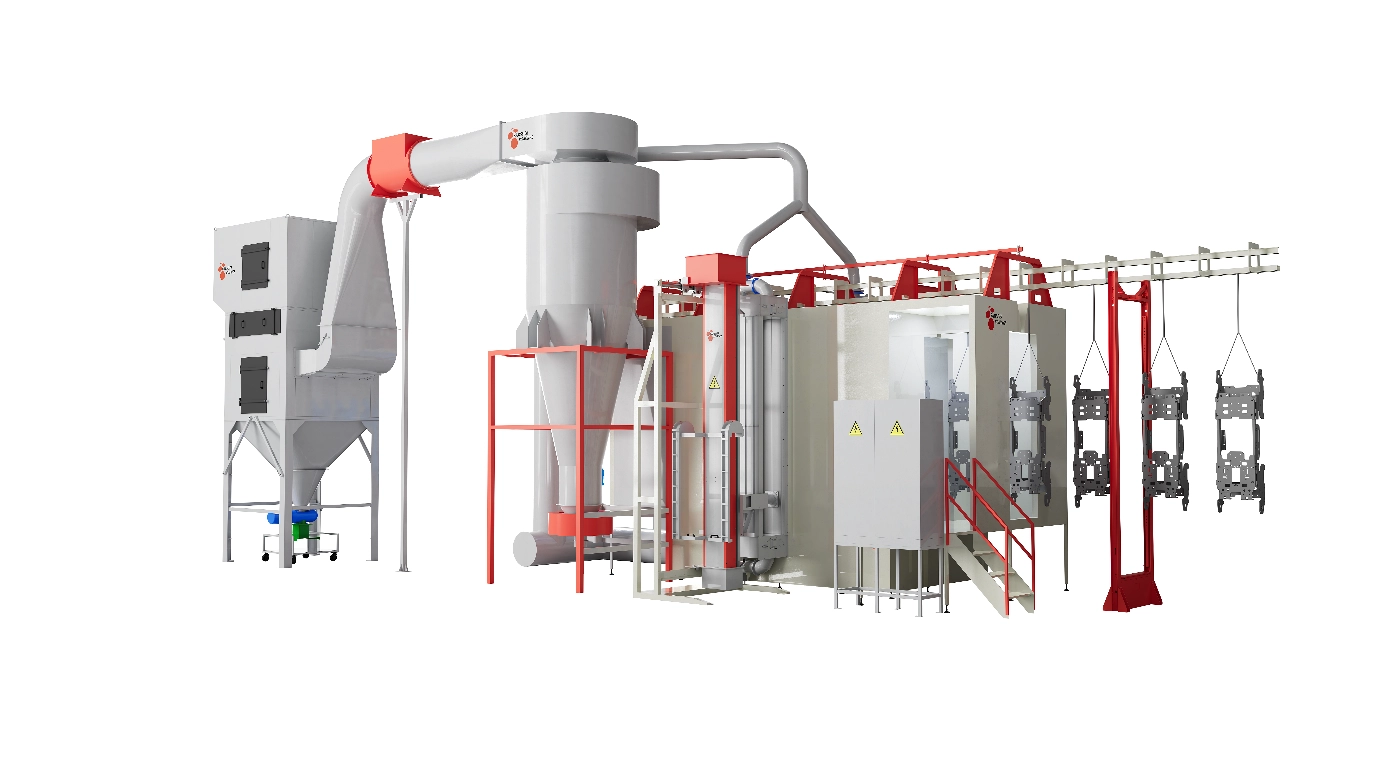
[1] https://www.pcimag.com/articles/109879-powder-coating-equipment-monitoring-from-gema
[2] https://www.scribd.com/document/813455547/%E8%8B%B1%E8%AF%AD%E8%AF%8D%E6%B1%87%E5%AD%A6%E5%AE%9E%E8%B7%B5
[3] https://proplate.pro/how-erp-software-can-solve-inventory-management-challenges-in-powder-coating/
[4] https://huggingface.co/facebook/xm_transformer_unity_hk-en/commit/e37fd5ab9c6faf7a9547972cf6dace1c144c49c8.diff?file=en_zh_spm.dict
[5] https://gosteelhead.com/powder-coating-software
[6] https://ia800600.us.archive.org/5/items/ittushu-2470/%E6%B8%85%E5%8D%8E%E5%A4%A7%E5%AD%A6%E5%9B%BE%E4%B9%A6%E9%A6%86-%E6%88%98%E7%96%AB%E7%89%88/H_%E8%AF%AD%E8%A8%80%E3%80%81%E6%96%87%E5%AD%97/12133_%E5%9B%BD%E9%99%85%E4%BA%A4%E6%B5%81%E8%8B%B1%E8%AF%AD%E9%98%85%E8%AF%BB%E8%BF%9B%E9%98%B6%E6%95%99%E7%A8%8B_text.pdf
[7] https://www.wagner-group.com/us/industry/products/powder-coating/complete-systems/
[8] https://www.scribd.com/document/498929761/%E5%8F%8C%E8%89%B2%E8%A1%A8%E8%A7%A3%E8%8B%B1%E8%AF%AD%E8%AF%8D%E6%B1%87
[9] https://www.powdercoatingonline.com/software-for-powder-coating/
[10] https://mdx.mdict.org/%E6%8C%89%E8%AF%8D%E5%85%B8%E8%AF%AD%E7%A7%8D%E6%9D%A5%E5%88%86%E7%B1%BB/%E8%8B%B1%E8%AF%AD/%E8%8B%B1%E8%AF%AD%E4%B8%93%E4%B8%9A%E8%AF%8D%E5%85%B8/%5B%E8%8B%B1-%E6%B1%89%5D/%5B%E8%8B%B1-%E6%B1%89%5D%206%E4%B8%87%E5%A4%9A%E4%B8%AA%E5%8F%A5%E5%AD%90%E9%A3%9E%E8%B7%836.0%E5%8F%A5%E5%BA%93%E5%AF%BC%E5%87%BA%EF%BC%88%E9%99%84%E6%BA%90%E6%96%87%E4%BB%B6%EF%BC%89/%5B%E8%8B%B1-%E6%B1%89%5D%206%E4%B8%87%E5%A4%9A%E4%B8%AA%E5%8F%A5%E5%AD%90%E9%A3%9E%E8%B7%836.0%E5%8F%A5%E5%BA%93%E5%AF%BC%E5%87%BA%EF%BC%88%E9%99%84%E6%BA%90%E6%96%87%E4%BB%B6%EF%BC%89.txt
Hot Tags: China, Global, OEM, private label, manufacturers, factory, suppliers, manufacturing company