Content Menu
● What Are Swinger Powder Coating Machines?
>> Benefits of Swinger Technology in Powder Coating
● Key Features of High-Performance Swinger Powder Coating Machines
>> 1. Advanced Spray Gun Technology
>> 2. Durable and Ergonomic Design
>> 3. Programmable Motion Control
>> 4. Integration with Automation and Robotics
>> 5. Powder Recovery and Booth Designs
● Leading Swinger Powder Coating Machines and Solutions
>> Nordson Encore Series
>> Sames Technologies Inogun M
>> Additional Considerations for Powder Coating Machines
● How to Select the Best Swinger Powder Coating Machine for Your Operation
>> Assess Production Volume and Part Complexity
>> Consider Powder Usage and Transfer Efficiency
>> Match Machine Capabilities to Product Geometry
>> Evaluate Maintenance and Support Services
● Maintenance Tips for Optimal Performance of Swinger Powder Coating Machines
● Frequently Asked Questions
Powder coating has become a preferred finishing method across many industries due to its durability, high-quality appearance, and environmental benefits. For manufacturing lines that require precision, efficiency, and flawless coverage, choosing the best swinger powder coating machines is critical to achieving high-performance finishes. This article explores the key features, technologies, and advantages of top swinger powder coating machines, guides on selecting the right equipment, and highlights maintenance tips to ensure optimal finishing results.
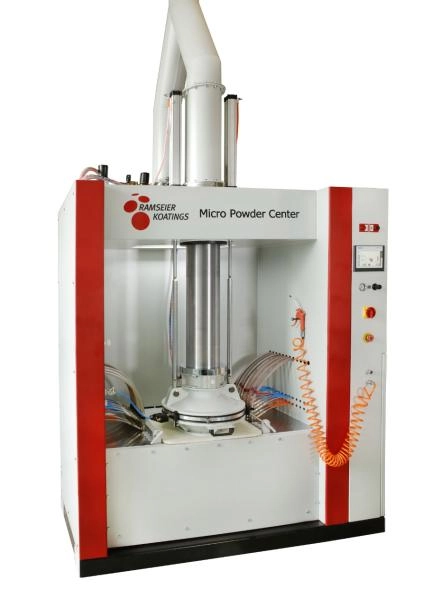
What Are Swinger Powder Coating Machines?
Swinger powder coating machines are advanced systems designed to coat complex parts by moving the spray gun or the parts in swinging or rotational motions. This movement ensures uniform powder coverage, even on difficult-to-reach surfaces, corners, and edges. Such machines may be manual, semi-automatic, or fully automatic and integrate with conveyors or robotic arms to boost productivity and consistency.
Benefits of Swinger Technology in Powder Coating
- Improved coverage: The swinging motion allows powder to reach recessed and contoured surfaces better than static guns.
- Higher efficiency: Minimal powder waste due to precise, controlled application.
- Consistent finishing: Reduces the need for manual touch-ups, leading to improved throughput and less rework.
- Flexibility: Adaptability across various product sizes, shapes, and coating thickness requirements.
Key Features of High-Performance Swinger Powder Coating Machines
Understanding the crucial features helps businesses invest wisely and meet their specific finishing demands.
1. Advanced Spray Gun Technology
Top swinger machines are equipped with spray guns that incorporate high voltage control units and electrostatic charge self-adjustments to optimize powder transfer. For instance, technologies like TEC5 technology allow the spray guns to adjust charge voltage based on powder flow rate and target distance, reducing overspray and enhancing transfer efficiency.
2. Durable and Ergonomic Design
The equipment balances operator comfort and durability — lightweight guns with ergonomic grips reduce fatigue during manual operation. Components such as cascade electrodes are designed for long life, suitable for heavy industrial use.
3. Programmable Motion Control
Automatic swinger powder coating systems often use sophisticated motion controllers to program swinging angles, speed, and spray cycles. This ensures the coating is accurately applied without overspray or missed spots, particularly important for complex-shaped parts or assembly lines requiring repeatability.
4. Integration with Automation and Robotics
Optimal finish quality is achieved by combining swinger guns with robotic or automatic conveyance systems. The gun swingers can be mounted on robotic arms or vertical/horizontal movers that adjust to product contours dynamically, ensuring uniform finishes and high productivity.
5. Powder Recovery and Booth Designs
High-performance systems include recovery booths with fast color change capabilities and powder recycling features. These booths are often designed with materials that prevent powder buildup, facilitating easy cleaning and reducing downtime during operations.
Leading Swinger Powder Coating Machines and Solutions
Several brands and models excel in delivering high-performance finishes due to innovative design and technology integration.
Nordson Encore Series
The Nordson Encore lineup offers both manual and automatic powder coating systems renowned for highest powder application efficiency and finish quality. The Encore HD spray gun system, with HDLV technology, produces a dense, low-velocity powder cloud for superior coverage on challenging parts. They also provide vertical and horizontal gun movers to optimize uniformity across complex parts.
The Dynamic Contouring Movers that accompany these guns allow accurate tracking and movement adapted to product geometry, minimizing manual intervention.
Sames Technologies Inogun M
The Inogun M manual powder gun stands out for its balanced and ergonomic design, combined with the TEC5 electronic control technology that optimizes powder transfer efficiency. This gun delivers a high wraparound effect, efficiently coating large parts and penetrating deep recesses. It reduces operator fatigue while improving finish consistency.
The Inogun M integrates with the Inobox or Inocontroller for precise air and voltage regulation, supporting both manual and automatic applications.
Additional Considerations for Powder Coating Machines
Along with gun and swinger mechanics, the type of powder used can impact finishing performance. For example:
- Polyester powders offer UV resistance suitable for exterior parts.
- Epoxy powders provide chemical and abrasion resistance but are more suited for indoor use.
- Hybrid powders blend epoxy and polyester benefits for appliance finishes.
- Specialty powders such as nylon (for flexibility and sound damping) and fluoropolymer (for non-stick, weather-resistant finishes) cater to niche requirements.
How to Select the Best Swinger Powder Coating Machine for Your Operation
Assess Production Volume and Part Complexity
High-volume production lines demand automated swinger systems with integration capabilities to maximize throughput. For smaller or customized batches, manual or semi-automatic swinger guns with ergonomic design may be preferable.
Consider Powder Usage and Transfer Efficiency
Machines that incorporate electrostatic self-adjustment technologies reduce powder waste and improve finish quality, lowering operating costs over time.
Match Machine Capabilities to Product Geometry
Complex parts require swingers with multi-axis motion control and the ability to maintain spray consistency over uneven surfaces.
Evaluate Maintenance and Support Services
Choose systems from manufacturers offering comprehensive technical support, training, and quick availability of spare parts and consumables to minimize downtime.
Maintenance Tips for Optimal Performance of Swinger Powder Coating Machines
- Regularly clean spray guns and booths to prevent powder clogging and buildup.
- Check and calibrate voltage and air pressure controls for consistent electrostatic charge.
- Inspect and replace wear parts like nozzles and electrodes timely.
- Maintain powder supply and recovery systems to avoid contamination and ensure smooth flow.
- Train operators adequately in handling ergonomic spray guns to reduce fatigue and errors.
Frequently Asked Questions
Q1: What is the advantage of a swinger powder coating machine over traditional guns?
A1: Swinger machines improve coverage uniformity on complex shapes through controlled swinging motions, reducing overspray and rework.
Q2: Can swinger powder coating guns be used manually and automatically?
A2: Yes, depending on the model, some swinger guns like the Inogun M support both manual operation and integration with automatic booths.
Q3: How does powder transfer efficiency affect coating quality?
A3: Higher transfer efficiency means more powder adheres to the part, resulting in better finish quality and less waste, lowering overall cost.
Q4: Are swinger powder coating machines suitable for outdoor products?
A4: When combined with suitable powders like polyester or fluoropolymer, swinger systems can produce durable outdoor finishes resistant to UV and weather.
Q5: What maintenance is critical for swinger powder coating machines?
A5: Regular cleaning, calibration of controls, timely replacement of wear parts, and proper powder handling ensure consistent performance and longevity.
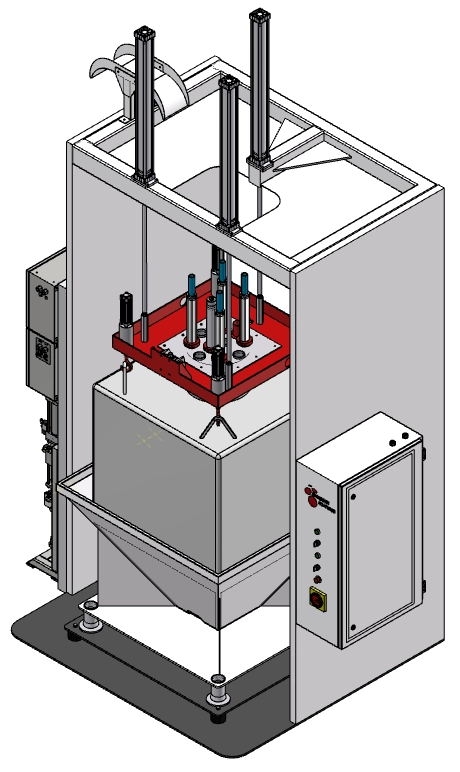
[1] https://www.nordson.com/en/divisions/industrial-coating-systems/application-solutions/powder-coating
[2] https://www.nordson.com/zh-cn/about-us/newsroom/industrial-coating-systems-news/nordson-powder-coating-in-the-united-kingdom
[3] https://www.sames.com/usa/en/product-inogun-M.html
[4] https://patents.google.com/patent/CN101096080A/zh
[5] https://www.youtube.com/watch?v=HdAbkHibxuY
[6] https://patents.google.com/patent/CN114555296A/zh
[7] https://reliantfinishingsystems.com
[8] https://patents.google.com/patent/CN113146464A/zh
[9] https://www.columbiacoatings.com/store/c/568-Equipment.aspx
[10] https://patents.google.com/patent/CN102876231A/zh
Hot Tags: China, Global, OEM, private label, manufacturers, factory, suppliers, manufacturing company