Content Menu
● Understanding the Basics: Powder Supply Systems vs. Centrifugal Systems
>> What is a Powder Supply System?
>> What are Centrifugal Systems?
● Key Performance Differences Between Powder Supply and Centrifugal Systems
>> Flow Rate and Pressure Behavior
>> Impact of Material Viscosity
>> Handling Powders and Bulk Solids
● Advantages of Powder Supply Systems Over Centrifugal Systems
>> Lower Maintenance and Increased Safety
>> Reduced Spillage and Dust Leakage
>> Enhanced Flexibility and Customization
>> Better Suitability for Viscous and Sensitive Materials
● Limitations and Challenges of Powder Supply Systems
>> Energy Efficiency Concerns
>> Dust Collection Requirements
>> Material Limitations
>> Safety Considerations for Combustible Powders
● When Do Centrifugal Systems Excel?
>> High Flow, Low Viscosity Applications
>> Simplicity and Cost-Effectiveness
>> Avoiding Cavitation and Dry Running
● Comparative Summary Table
● Can Powder Supply Systems Beat Centrifugal Systems?
● Related Questions and Answers
● Citations:
In industrial processes, the efficient and reliable transport of powders and fluids is critical. Two common technologies for moving materials are powder supply systems, often pneumatic or positive displacement-based, and centrifugal systems, including centrifugal pumps and blowers. This article explores whether a powder supply system can outperform centrifugal systems by examining their principles, advantages, limitations, and applications.
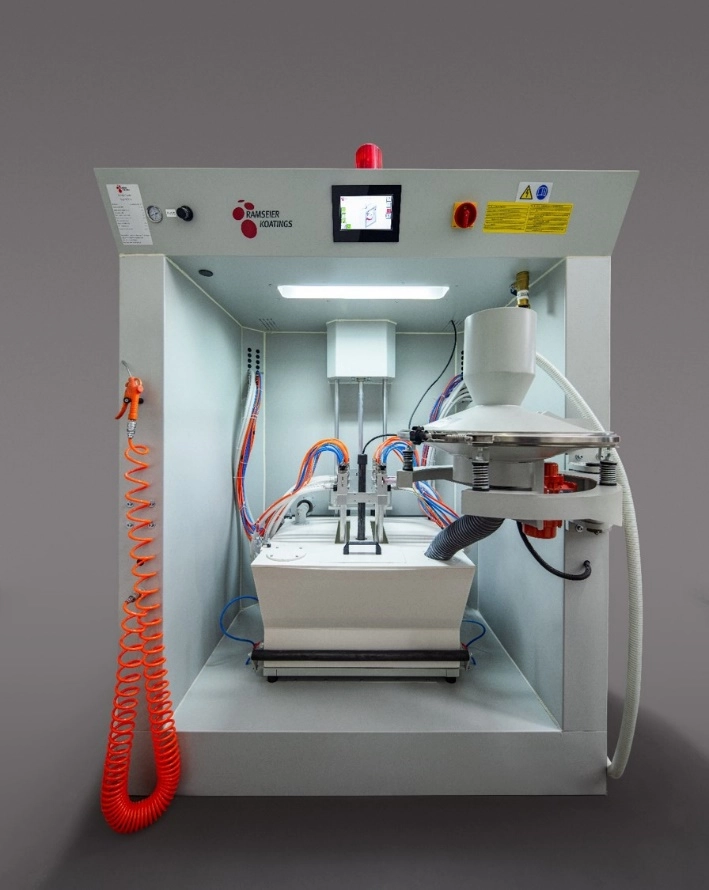
Understanding the Basics: Powder Supply Systems vs. Centrifugal Systems
What is a Powder Supply System?
Powder supply systems are designed to transport bulk powders through pipelines using various mechanisms, often pneumatic conveying. Pneumatic systems use air or gas streams to move powders in enclosed pipelines, offering flexibility and cleanliness. Positive displacement (PD) systems, including PD pumps and blowers, move a fixed volume of material per cycle, providing consistent flow regardless of pressure changes.
What are Centrifugal Systems?
Centrifugal systems include centrifugal pumps and blowers that move fluids or gases by imparting velocity through a rotating impeller. The kinetic energy from the impeller converts to pressure, creating flow. Centrifugal pumps are commonly used for liquids, while centrifugal blowers handle gases and air streams.
Key Performance Differences Between Powder Supply and Centrifugal Systems
Flow Rate and Pressure Behavior
Centrifugal pumps generate flow by increasing fluid velocity, but their flow rate decreases as discharge pressure rises. In contrast, positive displacement systems maintain nearly constant flow even as pressure increases because they displace a fixed volume per cycle. This makes PD systems more reliable under varying pressure conditions.
Impact of Material Viscosity
Viscosity significantly affects centrifugal pumps, which experience reduced flow rates as fluid viscosity increases. Conversely, PD pumps handle viscous fluids better, often delivering higher flow rates with increasing viscosity because viscous fluids reduce slip within the pump mechanism.
Handling Powders and Bulk Solids
Powder supply systems, especially pneumatic conveyors, excel at moving powders through enclosed pipelines, minimizing dust leakage and contamination. Centrifugal systems are typically designed for liquids or gases, making them less suitable for bulk powder transport. Pneumatic systems offer better sanitation and flexibility in routing powders within a plant.
Advantages of Powder Supply Systems Over Centrifugal Systems
Lower Maintenance and Increased Safety
Powder supply systems, particularly pneumatic conveyors, have fewer moving parts than mechanical centrifugal systems, resulting in lower maintenance requirements and reduced risk to operators.
Reduced Spillage and Dust Leakage
Enclosed pipelines in powder systems contain powders and dust effectively, improving plant cleanliness and reducing product loss compared to open or mechanical systems.
Enhanced Flexibility and Customization
Powder systems can be custom-designed to fit complex plant layouts, offering multiple feed and discharge points and longer conveying distances without significant space requirements.
Better Suitability for Viscous and Sensitive Materials
Positive displacement mechanisms in powder systems handle viscous or sticky materials better than centrifugal pumps, which struggle with such fluids.
Limitations and Challenges of Powder Supply Systems
Energy Efficiency Concerns
Pneumatic powder systems generally consume more energy than centrifugal systems because they rely on air streams to move materials, requiring higher power input to maintain pressure and flow.
Dust Collection Requirements
Because pneumatic systems use air to convey powders, they need robust dust collection and filtration at discharge points to separate product from the conveying air, adding complexity and cost.
Material Limitations
Certain powders with large particle sizes, high fat content, or stickiness can cause buildup and blockages in pneumatic systems, limiting their applicability.
Safety Considerations for Combustible Powders
Pneumatic conveying of combustible dusts requires special precautions to prevent deflagration and fire hazards, complicating system design and operation.
When Do Centrifugal Systems Excel?
High Flow, Low Viscosity Applications
Centrifugal pumps are ideal for moving large volumes of low-viscosity liquids at relatively low pressures efficiently and with simpler maintenance.
Simplicity and Cost-Effectiveness
Centrifugal pumps have fewer parts and are generally less expensive upfront compared to positive displacement pumps of similar size.
Avoiding Cavitation and Dry Running
While centrifugal pumps can suffer from cavitation and damage if run dry, proper system design and operation mitigate these risks effectively.
Comparative Summary Table
Feature | Powder Supply System (Pneumatic/PD) | Centrifugal System |
Flow Rate vs Pressure | Nearly constant flow under varying pressure | Flow decreases as pressure increases |
Viscosity Handling | Better with viscous/sticky materials | Reduced flow with higher viscosity |
Material Type | Powders, bulk solids, viscous fluids | Liquids and gases |
Maintenance | Lower due to fewer moving parts | Higher due to mechanical complexity |
Energy Efficiency | Generally less efficient | More energy efficient for liquids |
Dust and Contamination Control | Excellent (enclosed system) | Limited (open or semi-open systems) |
Safety for Combustible Dusts | Requires special design | Less applicable for powders |
Flexibility in Plant Layout | High (customizable pipelines) | Moderate (fixed piping and placement) |
Initial Cost | Moderate to high (custom design) | Generally lower for standard pumps |
Can Powder Supply Systems Beat Centrifugal Systems?
The answer depends on the specific application requirements:
- For transporting powders, bulk solids, and viscous fluids with minimal contamination and flexible routing, powder supply systems clearly outperform centrifugal systems.
- When handling large volumes of low-viscosity liquids at low pressure, centrifugal pumps are more energy-efficient and cost-effective.
- In environments where dust control, sanitation, and operator safety are priorities, pneumatic powder systems have significant advantages.
- For processes requiring consistent flow regardless of pressure fluctuations, positive displacement powder systems provide superior performance.
Therefore, powder supply systems can beat centrifugal systems in powder handling and specialized fluid transport scenarios, but centrifugal systems remain superior for high-volume, low-viscosity liquid pumping.
Related Questions and Answers
Q1: What types of materials are best suited for powder supply systems?
A1: Powder supply systems are ideal for fine powders, bulk solids, and viscous or sticky materials that require enclosed handling to prevent contamination and dust leakage.
Q2: Why do centrifugal pumps lose flow rate as pressure increases?
A2: Centrifugal pumps rely on velocity to generate flow, and as discharge pressure rises, the pump's ability to maintain flow decreases due to the physics of fluid dynamics.
Q3: Are pneumatic powder systems energy-efficient?
A3: Pneumatic systems generally consume more energy than centrifugal pumps because they use compressed air to move powders, requiring higher power input.
Q4: How do powder supply systems improve plant safety?
A4: By having fewer moving parts and enclosed pipelines, powder systems reduce operator exposure to moving machinery and minimize dust explosions risks when properly designed.
Q5: Can centrifugal pumps handle viscous fluids?
A5: Centrifugal pumps are less effective with viscous fluids as increased viscosity reduces flow rate and efficiency; positive displacement pumps are better suited for such fluids.
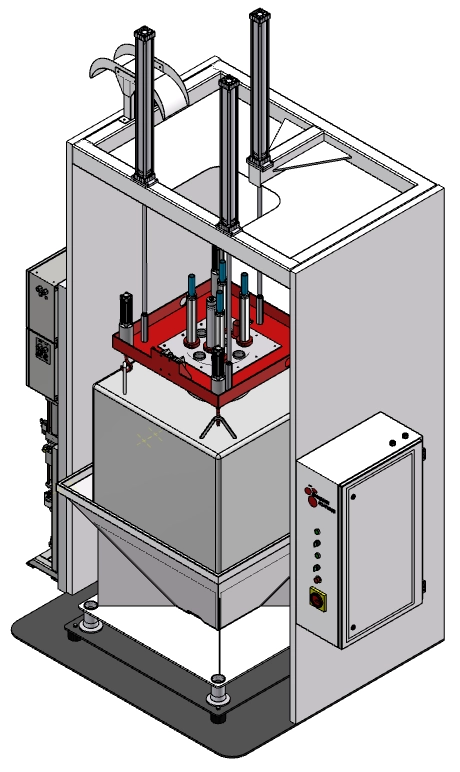
---
Citations:
[1] https://deltatsys.com/industry-expertise/pd-pump-centrifugal-pump/
[2] https://www.pneuvay.com.au/pneumatic-conveying/news/Centrifugal-blowers-vs-regenerative-blowers---The-BIG-difference/
[3] https://www.pumptec.com/blog/centrifugal-pumps-vs-positive-displacement-plunger-pumps
[4] https://www.waterandwastewater.com/positive-displacement-blower-vs-centrifugal/
[5] https://dragonproducts.com/positive-displacement-pump-vs-centrifugal-pump/
[6] https://www.powder-solutions.com/2016/09/26/the-pros-and-cons-of-pneumatic-conveying/
[7] https://www.cnblogs.com/luohenyueji/p/16990846.html
[8] https://techflow.net/articles/applications-and-benefits-of-a-powder-conveying-system
[9] https://shop.machinemfg.com/advantages-and-disadvantages-of-powder-metallurgy/
[10] https://www.cnblogs.com/yymn/p/16291346.html
[11] https://www.alphaprecisionpm.com/blog/advantages-and-disadvantages-of-powder-metallurgy
---
Hot Tags: China, Global, OEM, private label, manufacturers, factory, suppliers, manufacturing company